ผู้ผลิตเตาเผา เตาหลอม เตาสำหรับทดสอบขี้เถ้า (Ash Content Testing) สำหรับห้องแล็ป และเตาเผา เตาหลอมอุตสาหกรรมสำหรับการผลิตแก้ว เซรามิกส์ พลาสติก โลหะ เป็นต้น สามารถควบคุมอุณหภูมิในช่วง 30-3000 องศาเซลเซียส มีให้เลือกใช้หลากหลายขนาด
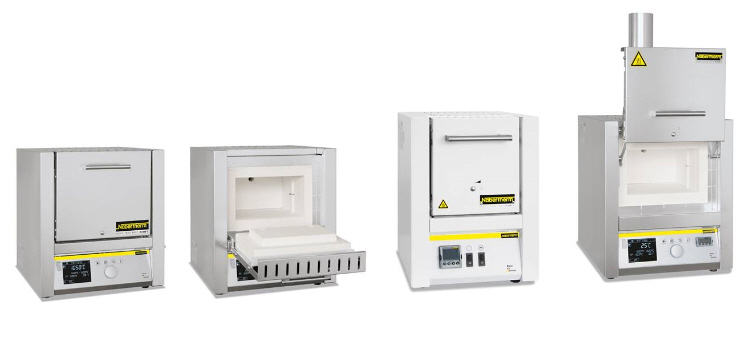
คลิ๊กด้านล่างเพื่อดูข้อมูลสินค้าเพิ่มเติม
Muffle/Preheating/Ashing Furnaces and
Accessories
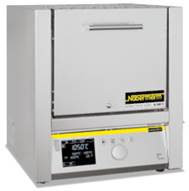 |
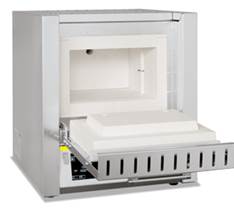 |
Muffle furnace L 3/12 |
Muffle furnace L 5/11 |
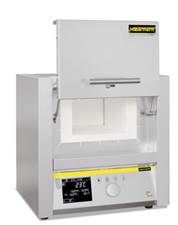
Muffle furnace LT 5/12
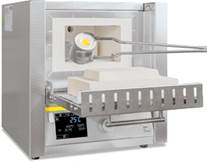
Muffle furnace L 3/11
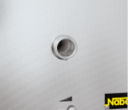
Observation hole in the door as additional equipment
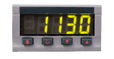
Over-temperature limiter
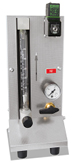
Gas supply system for non-flammable protective or reactive gas with shutoff valve and flow meter with regulator valve, optionally with magnetic valve
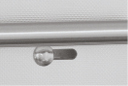
Adjustable air inlet integrated in the door
The muffle furnaces L 1/12 - LT 40/12 are the right choice for daily laboratory use. These models stand out for their excellent workmanship,
advanced and attractive design, and high level of reliability. The muffle furnaces come equipped with either a flap door or lift door at no extra charge.
- Tmax 1100 °C or 1200 °C
- Heating from two sides by ceramic heating plates (heating from three sides for muffle furnaces L 24/11 - LT 40/12)
- Ceramic heating plates with integral heating element which is safeguarded against fumes and splashing, and easy to replace
- Only fiber materials are used which are not classified as carcinogenic according to TRGS 905, class 1 or 2
- Housing made of sheets of textured stainless steel
- Dual shell housing for low external temperatures and high stability Optional flap door (L) which can be used as work platform or lift door (LT) with hot surface facing away from the operator
- Adjustable air inlet integrated in door (see illustration)
- Exhaust air outlet in rear wall of furnace
- Solid state relays provide for low-noise operation
- Defined application within the constraints of the operating instructions
- NTLog Basic for Nabertherm controller: recording of process data with USB-flash drive
Additional equipment
- Chimney, chimney with fan or catalytic converter (not for L 1)
- Over-temperature limiter with adjustable cutout temperature for thermal protection class 2 in accordance with EN 60519-2 as temperature limiter to protect the furnace and load
- Protective gas connection to purge with non-flammable protective or reaction gases (not available in combination with chimney, chimney with fan or catalytic converter)
- Observation hole in the door
- Manual or automatic gas supply system
- Process control and documentation via VCD software package for monitoring, documentation and
control
Available
Model Number ; Flap door : L 3/11, L 5/11, L 9/11, L 15/11, L 24/11, L 40/11, L
1/12, L 3/12, L 5/12, L 9/12, L 15/12, L 24/12, L 40/12
Lift door : LT 3/11, LT 5/11, LT 9/11, LT 15/11, LT 24/11, LT 40/11, LT 3/12, LT 5/12, LT 9/12,
LT 15/12,
LT 24/12, LT 40/12
Muffle
Furnaces Basic Models
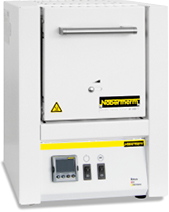 |
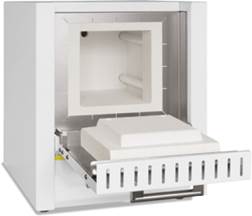 |
Muffle furnace LE 1/11 |
Muffle furnace LE 6/11 |
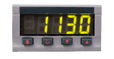
Over-temperature limiter
With their unbeatable price/performance ratio, these compact muffle furnaces are perfect for many applications in the laboratory. Quality
features like the dual shell furnace housing of rust-free stainless steel, their compact, lightweight constructions, or the heating elements encased in quartz glass tubes make these models reliable partners for your application.
- Tmax 1100 °C, working temperature 1050 °C Heating from two sides from heating elements in quartz glass tubes
- Maintenance-friendly replacement of heating elements and insulation
- Only fiber materials are used which are not classified as carcinogenic according to TRGS 905, class 1 or 2
- Housing made of sheets of textured stainless steel
- Dual shell housing for low external temperatures and high stability
- Flap door which can also be used as a work platform
- Exhaust air outlet in rear wall
- Solid state relays provide for low-noise operation
- Compact dimensions and light weight
- Controller mounted under the door to save space
- Defined application within the constraints of the operating instructions
Additional equipment
- Chimney, chimney with fan or catalytic converter (not for L 1)
- Over-temperature limiter with adjustable cutout temperature for thermal protection class 2 in accordance with EN 60519-2 as temperature limiter to protect the furnace and load
- Protective gas connection to purge with non-flammable protective or reaction gases
- Manual gas supply system
- Observation hole in the door
Available
Model Number ; LE 1/11, LE 2/11,
LE 6/11, LE 14/11
Muffle Furnaces with Brick
Insulation and Flap Door or Lift Door
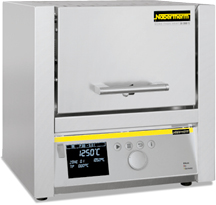 |
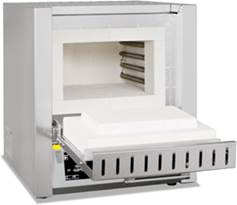 |
Muffle furnace LT 5/13 |
Muffle furnace L 9/13 |
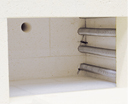
Furnace lining with high-quality lightweight refractory brick insulation
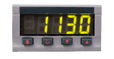
Over-temperature limiter
Heating elements on support tubes radiating freely into the
furnace chamber provide for particularly short heating times for these muffle
furnaces. Thanks to their robust lightweight refractory brick insulation, they
can reach a maximum working temperature of 1300 °C. These muffle furnaces thus
represent an interesting alternative to the familiar L(T) 3/11 models,
when you need particularly short heating times or a higher application
temperature.
- Tmax 1300 °C
- Heating from two
sides
- Heating elements on
support tubes ensure free heat radiation and a long service life
- Multi-layer
insulation with robust lightweight refractory bricks in the furnace
chamber
- Housing made of
sheets of textured stainless steel
- Dual shell housing
for low external temperatures and stability
- Optional flap door
(L) which can be used as work platform or lift door (LT) with hot surface
facing away from the operator
- Adjustable air
inlet in the furnace door
- Exhaust air outlet
in rear wall of furnace
- Solid state relays
provide for low-noise operation
- Defined application
within the constraints of the operating instructions
- NTLog Basic for
Nabertherm controller: recording of process data with USB-flash drive
Additional equipment
- Chimney, chimney
with fan or catalytic converter
- Over-temperature
limiter with adjustable cutout temperature for thermal protection class 2
in accordance with EN 60519-2 as temperature limiter to protect the
furnace and load
- Protective gas
connection to purge with non-flammable protective or reaction gases
- Manual or automatic
gas supply system
- Observation hole in
the door
- Process control and
documentation via VCD software package for monitoring, documentation and
control
Available
Model Number ; L, LT 5/13, L, LT
9/13, L, LT 15/13
Muffle Furnaces up to 1400
°C
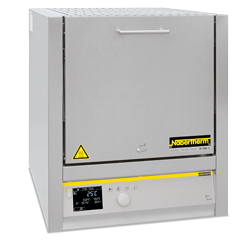 |
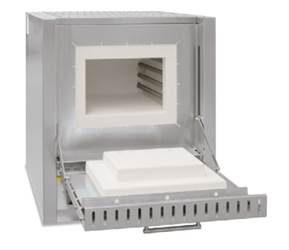 |
Muffle furnace L 9/14
|
Muffle furnace L 15/14
|
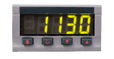
Over-temperature
limiter
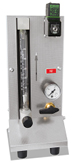
Gas supply
system for non-flammable protective or reactive gas with shutoff valve and flow
meter with regulator valve, optionally with magnetic valve
These models stand out for their excellent workmanship, advanced
and attractive design, and high level of reliability. Heating elements on
support tubes radiating freely into the furnace chamber provide for
particularly short heating times and a maximum temperature of 1400 °C.
These muffle furnaces are a good alternative to the familiar L(T) ../11 series
when higher application temperatures are needed.
- Tmax 1400 °C
- Heating from two sides
- Heating elements on support tubes ensure free heat radiation and a long service life
- Only fiber materials are used which are not classified as carcinogenic according to
TRGS 905, class 1 or 2
- Dual shell housing for low external temperatures and high stability
- Adjustable air inlet integrated in door
- Exhaust air outlet in rear wall of furnace
- Solid state relays provide for low-noise operation
- Defined application within the constraints of the operating instructions
- NTLog Basic for Nabertherm controller: recording of process data with USB-flash drive
Additional equipment
- Chimney, chimney with fan or catalytic converter
- Over-temperature limiter with adjustable cutout temperature for thermal protection class 2 in accordance with EN 60519-2 as temperature limiter to protect the furnace and load
- Protective gas connection to purge with non-flammable protective or reaction gases (not available in combination with chimney, chimney with fan or catalytic converter)
- Manual or automatic gas supply system
- Process control and documentation via VCD software package for monitoring, documentation and control
Available
Model Number ; L, LT 5/14, L, LT
9/14, L, LT 15/14
Muffle
Furnaces with Embedded Heating Elements in the Ceramic Muffle
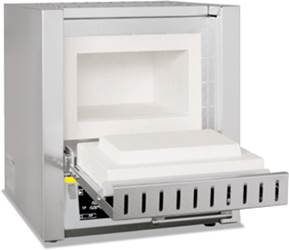 |
L 9/11/SKM |
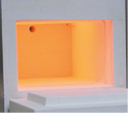
Muffle heated
from four sides
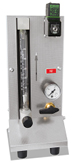
Gas supply
system for non-flammable protective or reactive gas with shutoff valve and flow
meter with regulator valve, optionally with magnetic valve
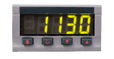
Over-temperature
limiter
We particularly recommend the muffle furnace L 9/11/SKM if your
application involves aggressive substances. The furnace has a ceramic muffle
with embedded heating from four sides. The muffle furnace thus combines a very
good temperature uniformity with excellent protection of the heating elements
from aggressive atmospheres. Another aspect is the smooth, nearly particle free
muffle (furnace door made of fiber insulation), an important quality feature
for some ashing processes.
- Tmax 1100 °C
- Muffle heated from
four sides
- Furnace chamber
with embedded ceramic muffle, high resistance to aggressive gasses and
vapours
- Dual shell housing
made of sheets of textured stainless steel
- Only fiber
materials are used which are not classified as carcinogenic according to
TRGS 905, class 1 or 2
- Optional flap door
(L) which can be used as work platform or lift door (LT) with hot surface
facing away from the operator
- Adjustable working
air inlet in the door
- Exhaust air outlet
in rear wall of furnace
- Solid state relays
provide for lownoise operation
- Defined application
within the constraints of the operating instructions
- NTLog Basic for
Nabertherm controller: recording of process data with USB-flash drive
Additional equipment
- Chimney, chimney
with fan or catalytic converter
- Over-temperature
limiter with adjustable cutout temperature for thermal protection class 2
in accordance with EN 60519-2 as temperature limiter to protect the
furnace and load
- Protective gas
connection to purge with non-flammable protective or reaction gases
- Manual or
automation gas supply system
- Observation hole in
the door
- Process control and
documentation via VCD software package for monitoring, documentation and
control
Available
Model Number ; L 9/11/SKM, LT
9/11/SKM
Ashing
Furnaces with Flap Door or Lift Door
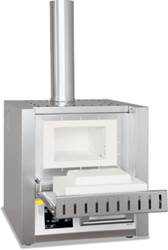 |
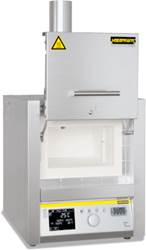 |
Ashing furnace LV 3/11 |
Ashing furnace LVT 9/11 |
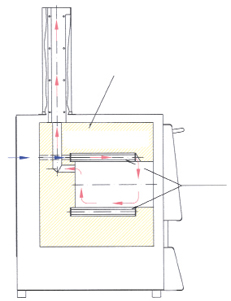
Air inlet
and exhaust flow principle in ashing furnaces
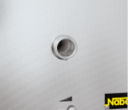
Observation
hole in the door as additional equipment
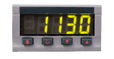
Over-temperature
limiter
The ashing furnaces LV 3/11 - LVT 15/11 are especially designed
for ashing in the laboratory. A special air intake and exhaust system allows
air exchange of more than 6 times per minute. Incoming air is preheated to
ensure a good temperature uniformity.
- Tmax 1100 °C
- Heating from two
sides
- Ceramic heating
plates with integral heating element which is safeguarded against fumes
and splashing, and easy to replace
- Air exchange of
more than 6 times per minute
- Good temperature
uniformity due to preheating of incoming air
- Only fiber
materials are used which are not classified as carcinogenic according to
TRGS 905, class 1 or 2
- Housing made of
sheets of textured stainless steel
- Dual shell housing
for low external temperatures and stability
- Optional flap door
(LV) which can be used as work platform or lift door (LVT) with hot
surface facing away from the operator
- Solid state relays
provide for lownoise operation
- Defined application
within the constraints of the operating instructions
- NTLog Basic for
Nabertherm controller: recording of process data with USB-flash drive
Additional equipment
- Over-temperature
limiter with adjustable cutout temperature for thermal protection class 2
in accordance with EN 60519-2 as temperature limiter to protect the
furnace and load
- Observation hole in
the door
- Process control and
documentation via VCD software package for monitoring, documentation and
control
Available
Model Number ;
Flap door : LV 3/11, LV 5/11,
LV 9/11, LV 15/11,
Lift door: LVT 3/11, LVT 5/11, LVT 9/11, LVT15/11
Ashing Furnaces with Integrated
Exhaust Gas Cleaning
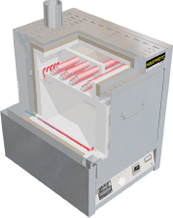 |
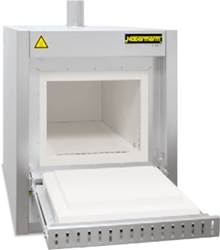 |
|
Ashing furnace L 40/11 BO |
The ashing furnace L ../11 BO is specially designed for
processes in which larger sample quantities have to be incinerated. Fields of
application are e.g. the ashing of food, thermal cleaning of injection molding
tools or the determination of annealing loss. Another application is the
debinding of ceramic products, e.g. after additive production.
The ashing furnaces have a passive safety system and integrated
exhaust gas post combustion. An exhaust gas fan extracts flue gases from the
furnace and simultaneously supplies fresh air to the furnace atmosphere with
the result that sufficient oxygen is always available for the incineration
process. The incoming air is guided behind the furnace heating and preheated to
ensure good temperature uniformity. Exhaust gases are led from the furnace
chamber to the integrated post combustion system, where they are postburned and
catalytically cleaned. Directly after the incineration process (up to max.
600 °C) a subsequent process up to max. 1100 °C can take place.
- Tmax 600 °C for the
incineration process
- Tmax 1100 °C for
the subsequent process
- Three-side heating
(both sides and bottom)
- Ceramic heating
plates with embedded heating wire
- Only fiber
materials are used which are not classified as carcinogenic according to
TRGS 905, class 1 or 2
- Dual shell housing
made of structured stainless steel provides for low outer temperature and
high stability
- Steel collecting
pan protects the bottom insulation
- Spring-assisted
closing of the furnace door (flap door) with mechanical locking against
unintentional opening
- Thermal/catalytic
post combustion, integrated in the exhaust channel, up to 600 °C in
function
- Temperature control
of post combustion can be set up to 850 °C
- Monitored exhaust
air
- Inlet-air preheated
through the bottom heating plate
- Over-temperature
limiter with adjustable cutout temperature for thermal protection class 2
in accordance with EN 60519-2 as temperature limiter to protect the
furnace and load
- Defined application
within the constraints of the operating instructions
- NTLog Basic for
Nabertherm controller: recording of process data with USB-flash drive
Additional equipment
- Process control and
documentation via VCD software package for monitoring, documentation and
control
Available Model Number ;
L 9/11 BO, L 24/11 BO, L 40/11 BO
Weighing Furnace incl. Scale and Software for Determination of
Combustion Loss
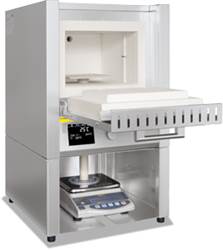 |
Weighing furnace L 9/11/SW |
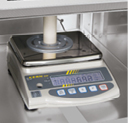
4 scales
available for different maximum weights and scaling areas
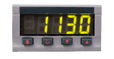
Over-temperature
limiter

Software
for documentation of the temperature curve and combustion loss using a PC
This weighing furnace with integrated precision scale and
software, was designed especially for combustion loss determination in the
laboratory. The determination of combustion loss is necessary, for instance,
when analyzing sludges and household garbage, and is also used in a variety of
technical processes for the evaluation of results. The difference between the
initial total mass and the combustion residue is the combustion loss. During
the process, the software included records both the temperature and the weight
loss.
- Tmax 1100 °C or
1200 °C
- Heating from two
sides
- Ceramic heating
plates with integral heating element which is safeguarded against fumes
and splashing, and easy to replace
- Only fiber
materials are used which are not classified as carcinogenic according to
TRGS 905, class 1 or 2
- Dual shell housing
made of sheets of textured stainless steel
- Optional flap door
(L) which can be used as work platform or lift door (LT) with hot surface
facing away from the operator
- Adjustable working
air inlet in the door
- Exhaust air outlet
in rear wall of furnace
- Solid state relays
provide for lownoise operation
- Delivery includes
base, ceramic plunger with base plate in the furnace lining, precision
scale and software package
- 4 scales available
for different maximum weights and scaling ranges
- Process control and
documentation for temperature and combustion loss via VCD software package
for monitoring, documentation and control
- Defined application
within the constraints of the operating instructions
Additional equipment
- Chimney, chimney
with fan or catalytic converter
- Over-temperature
limiter with adjustable cutout temperature for thermal protection class 2
in accordance with EN 60519-2 as temperature limiter to protect the
furnace and load
- Observation hole in
the door
Available
Model Number ;
flap door : L 9/11/SW, L 9/12/SW
Lift door : LT 9/11/SW, LT 9/12/SW
Exhaust
Systems/Accessories
* Note: If other controller types are used an adapter cable for
connection to mains supply has to be ordered separately. The device will be
activated by plugging in the socket.

|

|
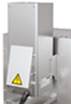
|
Chimney for connection to an
exhaust pipe.
|
Chimney with fan, to remove
exhaust gas from the furnace
better.
The B400 - P480 controllers
can be
used to activate the fan
automatically (not for
models L(T) 15..,
L 1/12, LE 1/11, LE 2/11).*
|
Catalytic
converter with fan for
removal of
organic components from
the exhaust
air. Organic components are catalytically oxidized at about 600 °C, broken
into carbon dioxide and water vapour. Irritating odors are thus largely
eliminated. The B400 - P480 controllers can be used to switch the catalytic
converter automatically (not for models L(T) 15.., L 1/12,
LE 1/11, LE 2/11).*
|
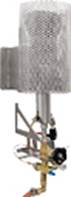
|

|

|
Exhaust torch to burn exhaust
gases which are generated during the process. The torch is gas-fired and will
be operated with propane gas. If a catalytic post combustion cannot be used
for the process this torch is recommended.
|
Square saggar for furnaces
LHTC and LHT, Tmax 1600 °C The load is placed in ceramic saggars for optimal
utilization of the furnace space. Up to three saggars can be stacked on top
of each other in the furnace. Each saggar has cut-outs for better
ventilation. The top saggar should be closed with a lid made of ceramics
also.
|
Round saggar (Ø 115 mm) for
furnaces LHT/LB, Tmax 1650 °C These saggars are perfectly suited for furnaces
LHT/LB. The load is placed in the saggars. Up to three saggars can be stacked
on top of each other in order to use the overall furnace chamber.
|
|
|
|
|
|
|
|
|
|
Additional equipment
- Base frame on
castors (not for assay furnace N 4/13 CUP)
- Process control and
documentation via VCD software package for monitoring, documentation and
control
Pit-type furnace with rolling lid
- For bigger charges
we offer pit-type furnaces as assay furnaces
Available
Model Number : N 4/13 CUP, N 8/13 CUP, N 25/13 CUP
Chamber Furnaces for Annealing, Hardening
and Brazing
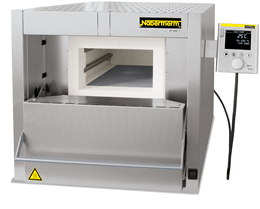
|
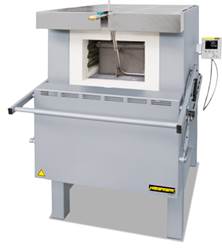
|
Chamber furnace N 7/H as table-top
model
|
Chamber furnace N 61/H
|
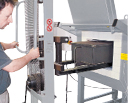
Working with protective gas boxes for a protective gas
atmosphere using a charging cart
To
withstand harsh use in the laboratory, e.g. when heat-treating metals, robust
insulation with light refractory bricks is necessary. The chamber furnaces N
7/H - N 87/H are a perfect fit to solve this problem. The furnaces can be
extended with a variety of accessories, like annealing boxes for operation
under protective gas, roller guides, or a cooling station with a quench tank.
Even high-performance applications like the annealing of titanium in medical
applications can be implemented without the use of expensive and complicated
annealing systems.
- Tmax 1280 °C
- Deep furnace
chamber with three-sides heating: from both side walls and bottom
- Heating elements on
support tubes ensure free heat radiation and a long service life
- Bottom heating
protected by heat-resistant SiC plate
- Low energy
consumption due to multi-layer insulation
- Exhaust opening in
the side of the furnace, or on back wall of chamber furnace N 31/H and
higher
- Base frame included
in the delivery, N 7/H - N 17/HR designed as table-top model
- Parallel guided
downward swinging door (user protected from heat radiation)
- Gas spring dampers
provide for easy door opening and closing
- Defined application
within the constraints of the operating instructions
- NTLog Basic for
Nabertherm controller: recording of process data with USB-flash drive
Available Model Number:
N 7/H, N 11/H, N 11/HR, N 17/HR
, N 31/H, N 41/H, N 61/H, N 87/H
Chamber Furnaces with Brick Insulation or Fiber Insulation up to 1400 °C
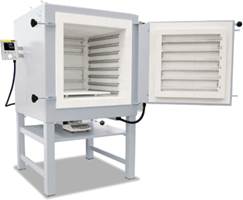 |
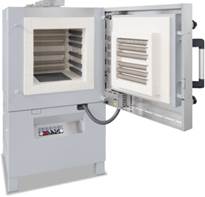 |
Chamber furnace LH 216/12SW with scale to
measure weight reduction during annealing |
Chamber furnace LF 60/14 with fresh air fan to
accelerate the cooling times |
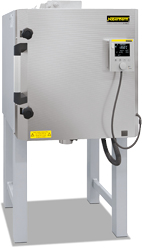
Chamber
furnace LH 30/14
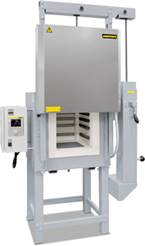
Chamber
furnace LH 30/12 with manual lift door
LF furnace design provides for
shorter heating and cooling times
The chamber furnaces LH 15/12 - LF 120/14 have been trusted for
many years as professional chamber furnaces for the laboratory. These furnaces
are available with either a robust insulation of light refractory bricks (LH
models) or with a combination insulation of refractory bricks in the corners
and low heat storage, quickly cooling fiber material (LF models). With a wide
variety of optional equipment, these chamber furnaces can be optimally adapted
to your processes.
- Tmax 1200 °C, 1300
°C, or 1400 °C
- Dual shell housing
with rear ventilation, provides for low shell temperatures
- High furnace
chamber with five-sided heating for very good temperature uniformity
- Heating elements on
support tubes ensure free heat radiation and a long service life
- Controller mounted
on furnace door and removable for comfortable operation
- Protection of
bottom heating and flat stacking surface provided by embedded SiC plate in
the floor
- LH models:
multi-layered insulation of light refractory bricks and special backup
insulation
- LF models: high-quality
fiber insulation with corner bricks for shorter heating and cooling times.
Only fiber materials are used which are not classified as carcinogenic
according to TRGS 905, class 1 or 2.
- Door with
brick-on-brick seal, hand fitted
- Short heating times
due to high installed power
- Self-supporting
arch for high stability and greatest possible protection against dust
- Quick lock on door
- Motor driven
exhaust air flap
- Freely adjustable
air inlet integrated in furnace floor
- Base included
- Defined application
within the constraints of the operating instructions
- NTLog Basic for
Nabertherm controller: recording of process data with USB-flash drive
Additional equipment
- Parallel swinging
door, pivots away from operator, for opening when hot
- Lift door with
electro-mechanic linear drive
- Separate
wall-mounting or floor standing cabinet for switchgear
- Cooling fan for
shorter cycle times
- Protective gas
connection to purge with non-flammable protective or reaction gases
- Manual or automatic
gas supply system
- Scale to measure
weight reduction during annealing
- Process control and
documentation via VCD software package or Nabertherm Control Center (NCC)
for monitoring, documentation and control
Available
Model Number : LH 15/12, LH 30/12, LH 60/12, LH 120/12, LH
216/12, LH 15/13, LH 30/13, LH 60/13,
LH 120/13, LH 216/13, LH 15/14, LH 30/14, LH 60/14, LH
120/14, LH 216/14 , LF 15/13, LF 30/13, LF 60/13, LF 120/13, LF 15/14, LF
30/14, LF 60/14, LF 120/14
High-Temperature Furnaces/Sintering
Furnaces
High-Temperature Furnaces with SiC
Rod Heating up to 1600 °C
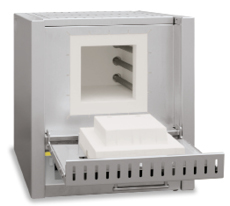 |
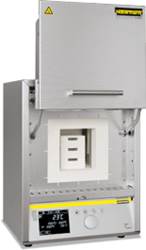 |
High-temperature furnace LHTC 08/16 |
High-temperature furnace LHTCT 01/16 |
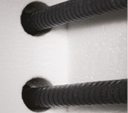
Furnace
chamber with high-quality fiber materials and SiC heating rods on both sides of
the furnace
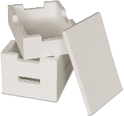
Saggars
with top lid

Over-temperature
limiter
These powerful laboratory muffle furnaces are available for
temperatures up to 1400 °C, 1500 °C, 1550 °C or 1600 °C. The
durability of the SiC rods in periodic use, in combination with their high
heating speed, make these high-temperature furnaces to all-rounders in the
laboratory. Heating times of 40 minutes to 1400 °C can be achieved,
depending on the furnace model and the conditions of use.
- Tmax 1400 °C, 1500
°C, 1550 °C or 1600 °C
- Working temperature
1500 °C (for high-temperature furnaces LHTC ../16), increased wear and
tear must be expected in case of working at higher temperatures
- Dual shell housing
made of textured stainless steel sheets with additional fan cooling for
low surface temperature
- Only fiber
materials are used which are not classified as carcinogenic according to
TRGS 905, class 1 or 2
- Optional flap door
(LHTC) which can be used as work platform or lift door (LHTCT) with hot
surface facing away from the operator (High-temperature furnace LHTCT
01/16 only with lift door)
- Switching system
with solid-state-relays, power tuned to the SiC rods
- Easy replacement of
heating rods
- Adjustable air
inlet opening, exhaust air opening in the roof
- Defined application
within the constraints of the operating instructions
- NTLog Basic for
Nabertherm controller: recording of process data with USB-flash drive
Additional equipment
- Over-temperature
limiter with adjustable cutout temperature for thermal protection class 2
in accordance with EN 60519-2 as temperature limiter to protect the
furnace and load
- Square saggar for
charging of up to three layers
- Lid for top saggar
- Manual or automatic
gas supply system
- Process control and
documentation via VCD software package for monitoring, documentation and
control
Available Model Number :
LHTC(T) 03/14, LHTC(T) 08/14, LHTC(T) 03/15,
LHTC(T) 08/15, LHTCT 01/16, LHTC(T) 03/16, LHTC(T) 08/16
High-Temperature Furnaces with MoSi2
Heating Elements up to 1800 °C
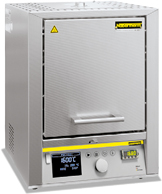 |
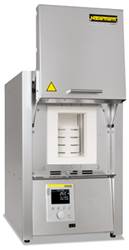 |
High-temperature furnace LHT 01/17 D |
High-temperature furnace LHT 03/17 D |
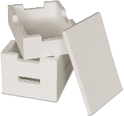
Saggars
with top lid

Over-temperature
limiter
Designed as tabletop models, these compact high-temperature
furnaces have a variety of advantages. The first-class workmanship using
high-quality materials, combined with ease of operation, make these furnaces
all-rounders in research and the laboratory. These high-temperature furnaces are
also perfectly suited for the sintering of technical ceramics, such as
zirconium oxide dental bridges.
- Tmax 1600 °C, 1750
°C, or 1800 °C
- High-quality
molybdenum disilicide heating elements
- Dual shell housing
made of textured stainless steel sheets with additional fan cooling for
low surface temperature
- Only fiber
materials are used which are not classified as carcinogenic according to
TRGS 905, class 1 or 2
- Compact design with
lift door, opening upwards
- Adjustable air
inlet
- Exhaust air opening
in the roof
- Type B thermocouple
- Defined application
within the constraints of the operating instructions
- NTLog Basic for
Nabertherm controller: recording of process data with USB-flash drive
Additional equipment
- Over-temperature
limiter with adjustable cutout temperature for thermal protection class 2
in accordance with EN 60519-2 as temperature limiter to protect the
furnace and load
- Square saggar for
charging of up to three layers
- Protective gas
connection to purge with non-flammable protective or reaction gases
- Manual or automatic
gas supply system
- Process control and
documentation via VCD software package for monitoring, documentation and
control
Available Model
Number : LHT 02/16, LHT 04/16, LHT 08/16, LHT 01/17 D, LHT 03/17
D, LHT 02/17, LHT 04/17,
LHT
08/17, LHT 02/18, LHT
04/18, LHT 08/18
High-Temperature
Bottom Loading Furnaces up to 1700 °C
,
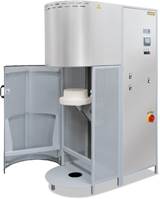 |
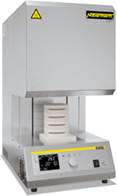 |
LHT 16/17 LB |
High-temperature furnace LHT 02/17 LB with a set of saggars |
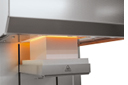
Electrically
driven lift-bottom

Saggar
The motor-driven lifting table significantly simplifies the
charging of the high-temperature furnaces LHT/LB. The heating all around the
cylindrical furnace chamber provides for an opitimal temperature uniformity.
For the tabletop models LHT 01/17 LB and LHT 02/17 LB the charge can be placed
in charge saggars made of technical ceramics. Up to three charge saggars can be
stacked on top of each other resulting in a high productivity. Due to its
volume the high-temperature furnace LHT 16/17 LB can also be used for
applications in production.
- Tmax 1650 °C, 1700
°C (LHT 16/17 LB)
- High-quality
heating elements made of molybdenum disilicide offer best possible
protection against chemical interaction between charge and heating
elements
- Only fiber
materials are used which are not classified as carcinogenic according to
TRGS 905, class 1 or 2
- Outstanding
temperature uniformity due to all-round furnace chamber heating
- Furnace chamber
with a volume of 1, 2 or 16 liters, table with large floor space
- Precise, motorized
toothed belt drive of the table with button operation
- Appealing, dual
shell stainless steel housing
- Exhaust air vent in
the roof
- Type S thermocouple
- Defined application
within the constraints of the operating instructions
- NTLog Basic for
Nabertherm controller: recording of process data with USB-flash drive
Additional equipment
- Over-temperature
limiter with adjustable cutout temperature for thermal protection class 2
in accordance with EN 60519-2 as temperature limiter to protect the
furnace and load
- Stackable saggars
for loading in up to two or three levels, depending on model
- Protective gas
connection to purge with non-flammable protective or reaction gases
- Manual or automatic
gas supply system
- Adjustable air
inlet through the floor
- Process control and
documentation via VCD software package for monitoring, documentation and
control
Available Model Number :
LHT 01/17 LB, LHT 02/17 LB, LHT 16/17 LB
High-Temperature Furnaces with Scale
for Determination of Combustion Loss and Thermogravimetric Analysis (TGA)
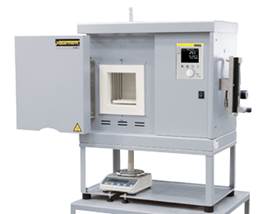
|
High-temperature furnace LHT
04/16 SW with scale for measuring weight reduction during annealing and with
gas supply system
|

Software for documentation of the temperature curve and
combustion loss using a PC
These high-temperature
furnaces were specially developed to determine combustion loss during annealing
and for thermogravimetric analysis (TGA) in the lab. The complete system
consists of the high-temperature furnace for 1600 °C or 1750 °C, a
table frame, precision scale with feedthroughs into the furnace and powerful
software for recording both the temperature curve and the weight loss over
time.
- Defined application
within the constraints of the operating instructions
- Technical
description of the furnaces: see models LHT 04/16 and LHT 04/17
- Description of the
weighing system: see models L 9/... SW
- Process control and
documentation for temperature and combustion loss via VCD software package
for monitoring, documentation and control
Available Model Number :
LHT 04/16 SW, LHT 04/17 SW
High-Temperature
Furnaces with Molybdenum Disilicide Heating Elements with Fiber Insulation up
to 1800 °C
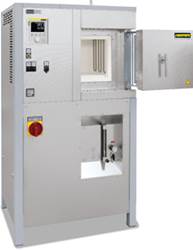
|
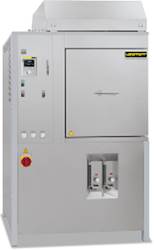
|
High-temperature furnace HT
16/18 with gas supply system
|
High-temperature furnace HT
160/17 with gas supply system
|
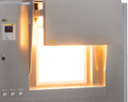
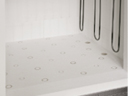
Reinforced floor as protection for bottom insulation for
high-temperature furnace HT 16/16 and higher
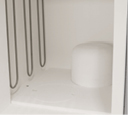
Inner
process top hat with gas injection through the furnace bottom protects the
furnace chamber against contamination and/or prevents chemical interaction
between the charge and heating elements
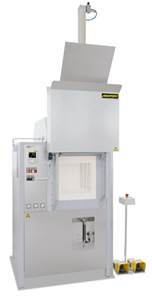
High-temperature furnace HT 64/16S with pneumatically
driven and parallel lift door
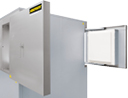
Two-door design for high-temperature furnaces > HT 276/..
Available
Model Number : HT 04/16, HT 08/16, HT 16/16, HT 40/16, HT
64/16, HT 128/16, HT 160/16, HT 276/16,
HT 450/16, HT 04/17, HT 08/17, HT 16/17, HT 40/17, HT
64/17, HT 128/17, HT 160/17, HT 276/17, HT 450/17, HT 04/18,
HT
08/18, HT 16/18, HT
40/18, HT 64/18, HT 128/18, HT 160/18, HT 276/18, HT 450/18,
High-Temperature
Furnaces with SiC Rod Heating up to 1550 °C
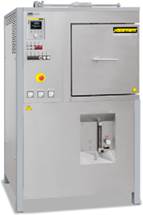
|
High-temperature furnace HTC
40/16
|
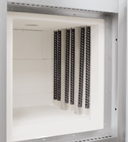
Vertically mounted SiC rods and optional perforated air inlet
tubes of the debinding system in a high-temperature furnace
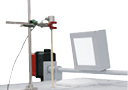
Exhaust air flap and charge thermocouple including a stand as
additional equipment
The
high-temperature furnaces HTC 16/16 - HTC 450/16 are heated by vertically hung
SiC rods, which makes them especially suitable for sintering processes up to a
maximum operating temperature of 1550 °C. For some processes, e.g. for
sintering zirconium oxide, the absence of interactivity between the charge and
the SiC rods, these models are more suitable than the alternatives heated with
molybdenum disilicide elements. The basic construction of these furnaces make
them comparable with the already familiar models in the HT product line and
they can be upgraded with the same additional equipment.
- Tmax 1550 °C
- Dual shell housing
with fan cooling for low shell temperatures
- Heating from both
sides via vertically mounted SiC rods
- High-quality fiber
insulation backed by special insulation
- Side insulation
constructed with tongue and groove blocks provides for low heat loss to
the outside
- Long-life roof
insulation with special suspension
- Only fiber
materials are used which are not classified as carcinogenic according to
TRGS 905, class 1 or 2
- Chain-guided
parallel swivel door for defined opening and closing of the door without
destroying the insulation
- Two-door design
(front/back) for high-temperature furnaces > HTC 276/..
- Labyrinth sealing
ensures the least possible temperature loss in the door area
- Reinforced floor as
protection for bottom insulation
- Exhaust air opening
in the furnace roof
- Heating elements
switched via SCR's
- Over-temperature
limiter with adjustable cutout temperature for thermal protection class 2
in accordance with EN 60519-2 as temperature limiter to protect the
furnace and load
- Defined application
within the constraints of the operating instructions
- NTLog Basic for
Nabertherm controller: recording of process data with USB-flash drive
Available Model
Number : HTC 16/16, HTC
40/16, HTC 64/16, HTC 128/16, HTC 160/16, HTC 276/16, HTC 450/16
High Temperature Furnaces with
Molybdenum Disilicide Heating Elements with Refractory Brick Insulation up to
1700 °C
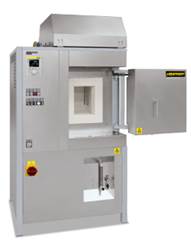 |
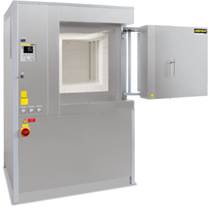 |
High-temperature furnace HFL 16/17 DB50 |
High-temperature furnace HFL 160/17 |
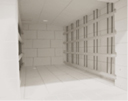
Protection
grid in front of heating elements prevent against mechanical damages
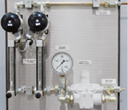
Gas supply
system for non-flammable protective or reaction gases
The high-temperature furnaces HFL 16/16 HFL 160/17 are
characterized by their lining with robust light refractory bricks. This version
is recommended for processes producing aggressive gases or acids, such as under
glass melting.
Standard equipment like
high-temperature furnaces HT, except:
- Tmax 1600 °C
or 1700 °C
- Robust refractory
brick insulation and special backing insulation
- Furnace floor made
of lightweight refractory bricks accommodates high charge weights
- Defined application
within the constraints of the operating instructions
- NTLog Basic for
Nabertherm controller: recording of process data with USB-flash drive
Available
Model Number : HFL 16/16, HFL 40/16, HFL 64/16, HFL 160/16,
HFL 16/17, HFL 40/17, HFL 64/17,
HFL 160/17
Ovens and Forced Convection Chamber
Furnaces
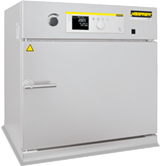 |
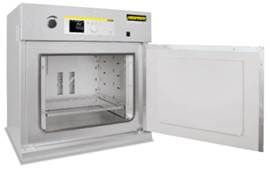 |
Oven TR 60 with adjustable fan speed |
Oven TR 240 |
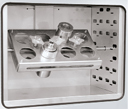
Electrical
rotating device as additional equipment
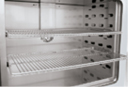
Extricable
metal grids to load the oven in different layers
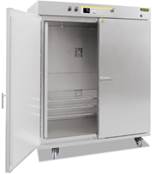
Oven TR
1050 with double door
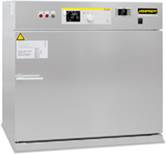
Oven
TR 120 LS with safety technology according to EN 1539 for charges
containing liquid solvents
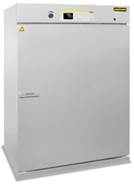
Oven TR
450
With their maximum working temperature of up to 300 °C and air
circulation, the ovens achieve a perfect temperature uniformity which is much
better than in ovens of most competitors. They can be used for various
applications such as e.g. drying, sterilizing or warm storing. Ample
warehousing of standard models provides for short delivery times.
- Tmax 300 °C
- Working temperature
range: + 5 °C above room temperature up to 300 °C
- Ovens TR 30 - TR
240 designed as tabletop models
- Ovens TR 450 and TR
1050 designed as floor standing models
- Horizontal, air
circulation results in temperature uniformity better than +/- 5 °C
- Stainless steel
chamber, alloy 304 (AISI)/(DIN material no. 1.4301), rust-resistant and
easy to clean
- Only fiber
materials are used which are not classified as carcinogenic according to
TRGS 905, class 1 or 2
- Large handle to
open and close the door
- Charging in
multiple layers possible using removeable grids (number of removeable
grids included, see table to the right)
- Large, wide-opening
swing door, hinged on the right with quick release for models TR 30 - TR
450
- Double swing door
with quick release for TR 1050
- TR 1050 equipped
transport rollers
- Infinitely
adjustable exhaust at the rear wall with operation from the front
- PID microprocessor
control with self-diagnosis system
- Solid state relays
provide for lownoise operation
- Defined application
within the constraints of the operating instructions
- NTLog Basic for
Nabertherm controller: recording of process data with USB-flash drive
Additional equipment
- Over-temperature
limiter with adjustable cutout temperature for thermal protection class 2
in accordance with EN 60519-2 as temperature limiter to protect the oven
and load
- Infinitely
adjustable fan speed of the air circulation fan
- Window for charge
observing
- Further removeable
grids with rails
- Side inlet
- Stainless steel
collecting pan to protect the furnace chamber
- Door hinges on the
left side
- Reinforced bottom
plate
- Safety technology
according to EN 1539 for charges containing liquid solvents
(TR .. LS) up to model TR 240 LS, achievable
temperature uniformity +/- 8 °C
- Transport castors
for model TR 450
- Various
modifications available for individual needs
- Upgrading available
to meet the quality requirements of AMS 2750 E or FDA
- Process control and
documentation via VCD software package for monitoring, documentation and
control
Available Model Number :
TR 30, TR 60, TR 60 LS, TR 120, TR 120 LS, TR 240, TR 240 LS, TR 450,
TR 1050
Chamber Ovens Electrically Heated or
Gas-Fired
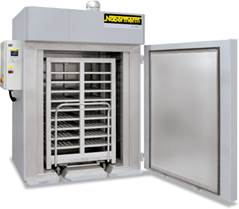 |
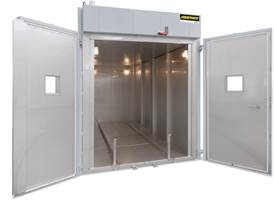 |
Chamber oven KTR 1500 with charging cart |
Chamber oven KTR 22500/S with chamber lightning and drive-in
tracks with insulated plugs which provide for an optimal temperature
uniformity |
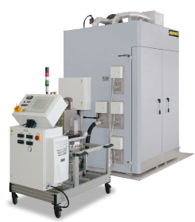
KTR 3100/S
for curing of composites in vacuum bags incl. pump and necessary connections in
the oven chamber
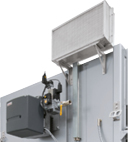
Direct
gas-firing at a chamber dryer
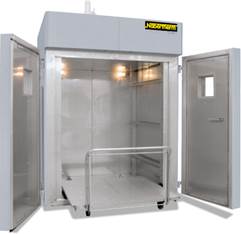
KTR 4500
with platform cart, inner lightning and observation windows
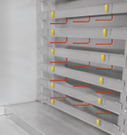
Adjustable
plate shutters to adapt the air guide to the charge
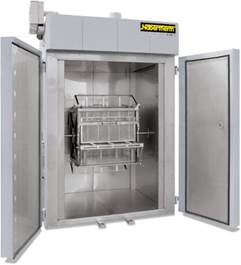
KTR 3100
DT with rotating system for tempering of silicone parts. Four baskets will be
charged in the frame and can be taken out separately
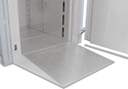
Drive-in
ramp
The chamber ovens of the KTR range can be used for complex
drying processes and heat treatment of charges to an application temperature of
260 °C. The high-performance air circulation enables optimum temperature
uniformity throughout the work space. A wide range of accessories allow the
chamber ovens to be modified to meet specific process requirements. The design
for the heat treatment of flammable materials in conformance with EN 1539
(NFPA 86) is available for all sizes.
- Tmax 260 °C
- Electrically heated
(via a heating register with integrated chrome steel heating elements) or
gas-fired (direct or indirect gas-fired including injection of the hot air
into the intake duct)
- Temperature
uniformity up to +/- 3 °C according to DIN 17052-1 (for
design wihout track cutouts)
- High-quality
mineral wool insulation provides for outer temperatures of < 25
°C above room temperature
- Only fiber
materials are used which are not classified as carcinogenic according to
TRGS 905, class 1 or 2
- High air exchange
for fast drying processes
- Double-wing door
for furnaces KTR 3100 and larger
- Over-temperature
limiter with adjustable cutout temperature for thermal protection class 2
in accordance with EN 60519-2 as temperature limiter to protect the oven
and load
- Incl. floor
insulation
- Defined application
within the constraints of the operating instructions
- NTLog Basic for
Nabertherm controller: recording of process data with USB-flash drive
Additional equipment
- Track cutouts for
level drive-in of charging cart
- Base frame to
charge the oven via a charging forklift
- Additional Door in
the back for charging from both sides or to use the oven as lock between
two rooms
- Fan system for
faster cooling with manual or motor-driven control of the exhaust flaps
- Programmed opening
and closing of exhaust air flaps
- Air circulation
with speed control, recommendable for processes with light or sensitive
charge
- Observation window
and furnace chamber lighting
- Safety technology
according to EN 1539 (NFPA 86) (models KTR .. LS) for charges
containing solvents
- Charging cart with
or without rack system
- Design for clean
room heat treatment processes
- Rotating systems
for tempering processes
- Process control and
documentation via VCD software package or Nabertherm Control Center (NCC)
for monitoring, documentation and control
Accessories
- Adjustable plate
shutters to adapt the air guide to the charge and improve temperature
uniformity
- Guide-in tracks and
shelves
- Shelves with 2/3
extraction with evenly distributed load on the whole shelve surface
- Platform cart in
combination with drive-in tracks
- Charging cart with
rack system in combination with drive-in tracks
- Sealing shoes for
ovens with drive-in tracks to improve temperature uniformity in the work
space
- All KTR-models are
also available with Tmax 300 °C.
Available Model Number :
KTR 1000 (LS), KTR 1500 (LS), KTR 3100 (LS), KTR 4500 (LS), KTR 6125
(LS), KTR 6250 (LS), KTR 8000 (LS), KTR 9000 (LS), KTR 12300 (LS), KTR 16000
(LS), KTR 21300 (LS), KTR 22500 (LS)
High-Temperature Ovens, Forced
Convection Chamber Furnaces
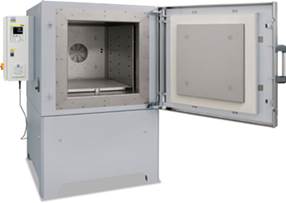
|
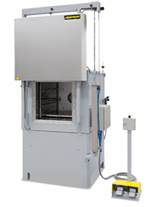
|
Forced convection chamber
furnace NA 250/45
|
Forced convection chamber
furnace NA 120/46 with lift door
|

Forced convection chamber furnace NA 15/65 as table-top
model
These
chamber furnaces with air circulation are characterized by their extremely high
temperature uniformity. Hence, they are especially suitable for processes such
as cooling, crystalizing, preheating, curing, but also for numerous processes
in tool making. Due to the modular concept, the forced convection furnaces can
be adjusted to the process requirements by adding suitable equipment.
- Tmax 450 °C, 650
°C, or 850 °C
- Horizontal air
circulation
- Swing door hinged
on the right
- Temperature
uniformity up to +/- 4 °C according to DIN 17052-1 (model NA 15/65 up to
+/- 5 °C)
- Optimum air flow
and temperature uniformity through high circulation rates
- One frame sheet and
rails for two additional trays included in the scope of delivery (NA 15/65
without frame sheet)
- Stainless steel
air-baffles in the furnace for optimum air circulation
- Base frame included
in the delivery, NA 15/65 designed as table-top model
- Air inlet and
exhaust air flaps as additional equipment for using as drying oven
- Defined application
within the constraints of the operating instructions
- NTLog Basic for
Nabertherm controller: recording of process data with USB-flash drive
Available
Model Number : NA 30/45, NA 60/45, NA 120/45, NA 250/45, NA
500/45, NA 15/65, NA 30/65, NA 60/65, NA 120/65, , NA 250/65, NA 500/65, N 30/85 HA, N 60/85 HA, N 120/85 HA, N 250/85
HA, N 500/85 HA
Sealed Forced Convection Chamber Furnaces NA-I and NA-SI
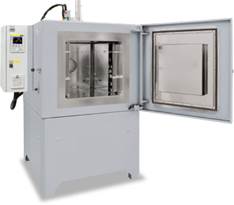 |
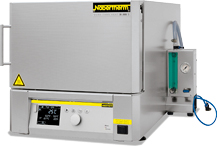 |
Forced convection chamber furnace NA 120/65 I |
Forced convection chamber furnace NA 15/65 I as tabletop
model with manual gas supply system |
Sealed forced convection chamber furnaces are suitable if a heat
treatment process up to 650 °C requires a protective gas atmosphere that does
not have to be completely oxygen free. The difference between the two variants
is that the I-model only has a sealed outer housing while the SI-model has a
welded inner box, which further reduces the residual oxygen concentration.
NA-I design Like
forced convection chamber furnaces < 675 l (page 34) with the following
changes
- Tmax 450 °C and 650
°C
- Silicone door seal
- Furnace housing
sealed with silicone
- Protective gas
connection in the back wall
- Defined application
within the constraints of the operating instructions
- Residual oxygen
concentration < 1 % depending on the volume and type of protective
gas
- For non-flammable
protective and reaction gases such as argon, nitrogen, and forming gas
(national regulations must be considered)
NA-SI design Additional
features
- Tmax 650 °C
- Welded inner
housing
- 2-sided heating and
air circulation
- Door sealed with
seal gas
- Sealed connection
to circulation motor
- Gas inlet via
circulator shaft
- Defined application
within the constraints of the operating instructions
- Residual oxygen
concentration to 0.1 % depending on the volume and type of protective
gas
- For non-flammable
protective and reaction gases such as argon, nitrogen, and forming gas
(national regulations must be considered)
Available
Model Number : NA 30/45 I, NA 60/45 I, NA 120/45 I, NA
250/45 I, NA 500/45 I, NA 675/45 I, NA 15/65 I1, NA 30/65 I, N A 60/65 I (SI), NA 120/65 I (SI), NA 250/65 I (SI), NA 500/65
I (SI), NA 675/65 I
Chamber Furnaces for Processes with High Vaporization Rates
of Organic Matter or for Thermal Cleaning by Ashing Electrically Heated or
Gas-Fired
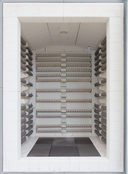
Chamber
furnace N 650/14 BO with ignition burner
The chamber furnaces of the model series N(B) .. BO
are used for processes with large amounts of organic matters or high
vaporization rates. These models can be used for products which are insensitive
against temporarily uncontrolled temperature increases. Processes in which the
product or contaminations on the product are ashed by ignition can be also
carried out safely in this type of chamber furnace. Examples include residual
wax removal of pouring clustersfollowed by sintering, or thermal cleaning of
oxide catalytic honey combs from soot or fuel residues. The electrically heated
N...BO furnaces can be used for processes with exact temperature control and
uniformity. For safety reasons, they are equipped with an integrated gas torch
for igniting the flammable components in the gas mixture. The accumulation of
flammable components is avoided and their safe combustion is ensured.
The gas-fired NB…BO furnaces are designed for processes which
require a heat-up time to temperatures > 500 °C
The burning of unwanted organic ingrediants can take place at
temperatures > 500 °C. Following this, a subsequent process can take place
up to max. 1400 °C (electrically) or up to 1000 °C (gas-fired).
For safety, the furnace door locks after the program was started
and cannot be opened again until the temperature has dropped below a defined
value. In case of burner malfunction or gas shortage the process is aborted.
Chamber furnaces N 100 BO - N
650/14 BO, electrically heated and gas-fired ignition flame
- Tmax 1000 °C or
1400 °C
- Only fiber
materials are used which are not classified as carcinogenic according to
TRGS 905, class 1 or 2
- Standard sizes up
to 650 liters furnace chamber, additional sizes on request
- Exhaust hood
- Fully automatic
temperature control
- Optional thermal
afterburning
- Ignition flame using
natural gas or liquid gas (LPG)
- Defined application
within the constraints of the operating instructions
Chamber furnaces models NB 300 BO
and NB 650 BO, gas-fired
- Tmax 1000 °C
- Only fiber
materials are used which are not classified as carcinogenic according to
TRGS 905, class 1 or 2
- Standard sizes up
to 650 liters furnace chamber, additional sizes on request
- Integrated thermal
afterburning
- Gas burners
operating with natural gas or liquid gas (LPG)
- Defined application
within the constraints of the operating instructions
Available Model Number :
N 100 BO, N 300 BO, N 300/14 BO, N 650/14 BO, NB 300 BO, NB 650 BO
Clean Room Solutions
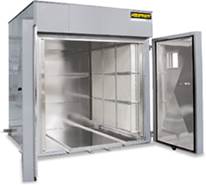
|
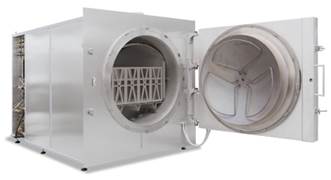
|
KTR 8000 designed as a
production oven in the clean room with filters for air circulation
|
Hot-wall retort furnace NRA
1700/06 with charging frame for installation in grey room with charging door
in clean room
|
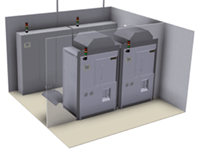
High-temperature furnace with loading from the clean room;
switchgear and furnace installed in grey room
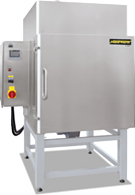
Forced convection chamber oven NAC 250/45 with clean room specs
Clean room
applications impose particularly high requirements to the design of the chosen
furnace. If the complete furnace is operated in a clean room an essential
contamination of the clean room atmosphere must be avoided. Especially, the
particle contamination must be reduced to a minimum.
The
specific application determines the choice of the required furnace technology.
In many cases forced convection furnaces are required to achieve the necessary
temperature uniformity at lower temperatures. For higher temperatures,
Nabertherm has also delivered many furnaces with radiant heating.
Furnace Installation in the Clean Room
If the
complete furnace is supposed to be positioned in the clean room, then it is
important that both the furnace chamber and the furnace housing as well as the
controls provide for good protection against contamination. Surfaces must be
easy to clean. The furnace chamber is tightly sealed to the insulation behind
it. If necessary, additional equipment such as filters for the fresh air supply
or the air circulation in the furnace can be used to improve the cleanliness
class. It is recommended to install the switchgear and the furnace controls
outside the clean room.
Furnace Installation in the Grey Room, Furnace Charging from the
Clean Room
Optimal
results with respect to cleanness will be achieved by placing the furnace in
the grey room with charging from the clean room. This significantly reduces the
amount of costly space needed in the clean room to a minimum. The front and the
furnace interior in the clean room are designed for easy cleaning. With this
configuration even the highest clean room classes can be achieved.
Sluice Furnace between Grey Room and Clean Room
Logistics
between clean room and grey room can often be easily sorted out. Lock furnaces
with one door in the grey room and the other door in the clean room are the
perfect choice for these applications. The inner chamber as well as the furnace
front in the clean room will be especially designed for lowest particle contamination.
Please
contact us if you are looking for a heat treatment solution under clean room
conditions. We would be pleased to quote for the oven or furnace model that
meets best your requirements.
Tube Furnaces and Accessories
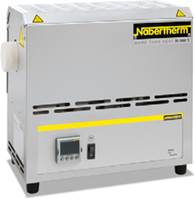 |
RD 30/200/11 |

Over-temperature
limiter
The RD tube furnaces convince with their unbeatable
price-performance ratio, very compact outer dimensions and their low weight.
These all-rounders are equipped with a working tube which also serves as
support for the heating wires. Thus, the working tube is part of the furnace
heating which has the advantage that the furnaces achieve very high heat-up
rates. The tube furnaces can be supplied for 1100 °C or 1300 °C. Both models
are designed for horizontal application. If the customer requires protective
gas atmosphere, a separate working tube incl. gas supply system 1, e.g. made of
quartz glass, must be inserted in the working tube.
- Tmax 1100 °C or
1300 °C
- Dual shell housing
made of sheets of textured stainless steel
- Only fiber
materials are used which are not classified as carcinogenic according to
TRGS 905, class 1 or 2
- Inner diameter of
the tube: 30 mm, heated length: 200 mm
- Working tube made
of C 530 material including two fiber plugs as standard
- Thermocouple type K
(1100 °C) or type S (1300 °C)
- Solid state relays
provide for low-noise operation of the heating
- Heating wires wound
directly around the working tube resulting in very fast heat-up rates
- Defined application
within the constraints of the operating instructions
Additional equipment
- Over-temperature
limiter with adjustable cutout temperature for thermal protection class 2
in accordance with EN 60519-2 as temperature limiter to protect the
furnace and load
- Gas supply system
for non-flammable protective or reactive gas
Available Model Number :
RD 30/200/11, RD 30/200/13
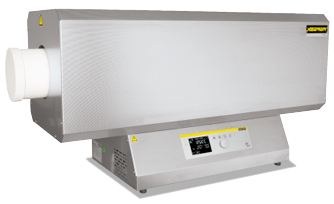 |
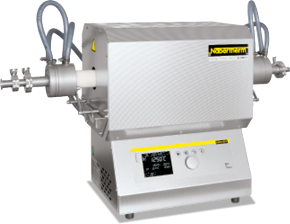 |
Tube furnace R 170/1000/13 |
Tube furnace R 50/250/13 with gas supply system 2 |
These compact tube furnaces with integrated control systems can
be used universally for many processes. Equipped with a standard working tube
of C 530 ceramic and two fiber plugs, these tube furnaces have an
unbeatable price/performance ratio.
- Tmax 1200 °C or
1300 °C
- Single-zoned design
as standard
- Dual shell housing
made of sheets of textured stainless steel
- Only fiber
materials are used which are not classified as carcinogenic according to
TRGS 905, class 1 or 2
- Outer tube diameter
of 50 mm to 170 mm, heated length from 250 mm to 1000 mm
- Working tube of C
530 ceramic including two fiber plugs as standard equipment
- Tmax 1200 °C: Type
N thermocouple
- Tmax 1300 °C: Type
S thermocouple
- Solid state relays
provide for lownoise operation
- Defined application
within the constraints of the operating instructions
- NTLog Basic for
Nabertherm controller: recording of process data with USB-flash drive
Additional equipment
- Over-temperature
limiter with adjustable cutout temperature for thermal protection class 2
in accordance with EN 60519-2 as temperature limiter to protect the
furnace and load
- Charge control with
temperature measurement in the working tube and in the furnace chamber
outside the tube
- Three-zoned design
(heated length from 500 mm)
- Gas supply systems
for protective gas or vacuum operation
- Process control and
documentation via VCD software package for monitoring, documentation and
control
Available Model Number :
R 50/250/12, R 50/500/12, R 120/500/12, R 170/750/12, R
170/1000/12, R 50/250/13, R 50/500/13, R 120/500/13, R 170/750/13, R
170/1000/13
Tube Furnaces with Stand for
Horizontal or Vertical Operation
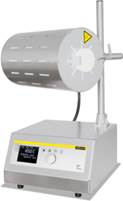
|
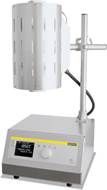
|
Tube furnace RT 50-250/11
|
Tube furnace RT 50-250/13
|
These
compact tube furnaces are used when laboratory experiments must be performed horizontally,
vertically, or at specific angles. The ability to configure the angle of tilt
and the working height, and their compact design, also make these tube furnaces
suitable for integration into existing process systems.
- Tmax 1100 °C, 1300
°C, or 1500 °C
- Compact design
- Only fiber
materials are used which are not classified as carcinogenic according to
TRGS 905, class 1 or 2
- Vertical or
horizontal operation freely adjustable
- Working height
freely adjustable
- Working tube made
of C 530 ceramic
- Type S thermocouple
- Operation also
possible separate from stand if safety guidelines are observed
- Control system
integrated in furnace base
- Defined application
within the constraints of the operating instructions
- NTLog Basic for
Nabertherm controller: recording of process data with USB-flash drive
Available Model Number :
RT 50-250/11 , RT 50-250/13, RT
30-200/15
High-Temperature Tube Furnaces with
SiC Rod Heating Gas Atmosphere or Vacuum
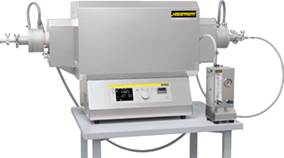 |
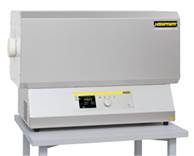 |
Tube furnace RHTC 80-230/15 with manual gas supply system |
Tube furnace RHTC 80-450/15 |
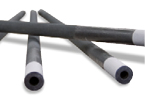
SiC rod
heating
These compact tube furnaces with SiC rod heating and integrated
switchgear and controller can be used universally for many processes. With an
easy to replace working tube as well as additional standard equipment options,
these furnaces are flexible and can be used for a wide range of applications.
The high-quality fiber insulation ensures fast heating and cooling times. The
SiC heating rods installed parallel to the working tube ensure excellent
temperature uniformity. The price-performance ratio for this temperature range
is unbeatable.
- Tmax 1500 °C
- Dual shell housing
made of sheets of textured stainless steel
- Only fiber
materials are used which are not classified as carcinogenic according to
TRGS 905, class 1 or 2
- Active cooling of
housing for low surface temperatures
- Type S thermocouple
- Solid state relays
provide for low-noise operation
- Prepared for
assembly of working tubes with water-cooled flanges
- Ceramic tube, C 799
quality
- Defined application
within the constraints of the operating instructions
- NTLog Basic for
Nabertherm controller: recording of process data with USB-flash drive
Additional equipment
- Over-temperature
limiter with adjustable cutout temperature for thermal protection class 2
in accordance with EN 60519-2 as temperature limiter to protect the
furnace and load
- Charge control with
temperature measurement in the working tube and in the furnace chamber
outside the tube
- Fiber plugs
- Check valve at gas
outlet avoids intrusion of false air
- Working tubes for
operation with water-cooled flanges
- Display of inner
tube temperature with additional thermocouple
- Alternative gas
supply systems for protective gas or vacuum operation
- Process control and
documentation via VCD software package for monitoring, documentation and
control
Available Model Number :
RHTC 80-230/15, RHTC 80-450/15, RHTC 80-710/15
High-Temperature Tube Furnaces for
Horizontal and Vertical Operation up to 1800 °C Gas Atmosphere or Vacuum
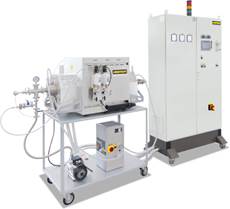 |
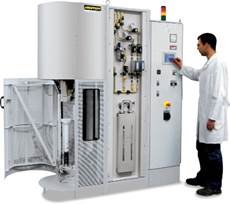 |
Tube furnace RHTH 120/600/17 |
Tube furnace RHTV 120/480/16 LBS with working tube closed at
one side, protective gas and vacuum option as well as with electric screw
drive of the lift table |
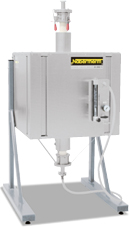
RHTV
50/150/17 vertical tube furnace with stand and gas supply system 2 as additional
equipment
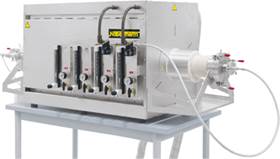
Tube
furnace RHTH 120/600/18
The high-temperature tube furnaces are available in either
horizontal (type RHTH) or vertical (type RHTV) designs. High-quality insulation
materials made of vacuum-formed fiber plates enable energy-saving operation and
a fast heating time due to low heat storage and heat conductivity. By using
different gas supply systems, operations can be performed under non-flammable
or flammable protective or reactive gases or under vacuum.
- Tmax 1600 °C, 1700
°C, or 1800 °C
- MoSi2 heating
elements, mounted vertically for easy replacement
- Insulation with
vacuum-formed ceramic fiber plates
- Only fiber
materials are used which are not classified as carcinogenic according to
TRGS 905, class 1 or 2
- Rectangular outer
housing with slots for convection cooling
- Tube furnaces RHTV
with frame for vertical operation
- Dual shell housing
made of sheets of textured stainless steel
- Ceramic working
tube made of material C 799 incl. fiber plugs for operation under air
- Type B thermocouple
- Power unit with
low-voltage transformer and thyristor
- Over-temperature
limiter with adjustable cutout temperature for thermal protection class 2
in accordance with EN 60519-2 as temperature limiter to protect the
furnace and load and with selectable maximum temperature gradient as tube
protection
- Switchgear and
control unit separate from furnace in separate floor standing cabinet
- Defined application
within the constraints of the operating instructions
- NTLog Basic for
Nabertherm controller: recording of process data with USB-flash drive
Additional equipment
- Charge control with
temperature measurement in the working tube and in the furnace chamber
outside the tube
- Display of inner
tube temperature with additional thermocouple
- Gas tight flanges
for protective gas and vacuum operation
- Manual or automatic
gas supply system
- Three-zone control
for optimization of temperature uniformity (only tube furnaces RHTH)
- Check valve at gas
outlet avoids intrusion of false air
- Process control and
documentation via VCD software package or Nabertherm Control Center (NCC)
for monitoring, documentation and control
Available Model Number ;
Horizontal
design : RHTH 50/150/.., RHTH 80/300/.., RHTH
120/600/.
Vertical
design : RHTV 50/150/.., RHTV 80/300/.., RHTV 120/600/..
Horizontal or Vertical Operation up
to 1300 °C Gas Atmosphere or Vacuum
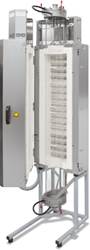 |
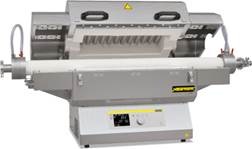 |
Tube furnace RSV 170/1000/11 with gas supply system 2 |
Tube furnace RSH 80/500/13 with gas tight tube and
water-cooled flanges |
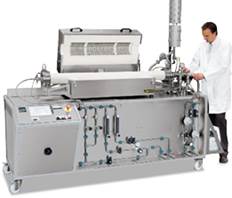
Tube
furnace RS 120/750/13 with gas supply system 4, hydrogen applications
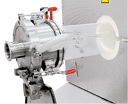
Quartz
glass and flanges for protective gas operation as optional equipment
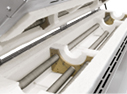
Tube
furnace RSH 120/1000/11S, three-zone controlled, incl. zone separators to reach
a temperature gradient
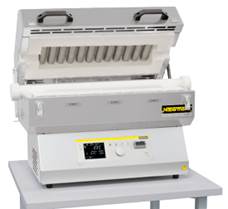
Tube furnace
RSH 50/500/13
These tube furnaces can be used for horizontal (RSH) or vertical
(RSV) operation. The split-type design makes it easy to change the working
tube. It allows for a comfortable exchange of various working tubes (e.g.
working tubes made of different materials).
Using the wide range of accessories these professional tube
furnaces can be optimally tailored to your process. By upgrading the furnaces
with different gas supply systems the operation in a protective gas atmosphere,
under vacuum or under flammable protective or reactive gases is possible.
Besides convenient standard controllers for process control modern PLC control
systems are also available.
- Tmax 1100 °C or
1300 °C
- Dual shell housing
made of sheets of textured stainless steel
- Only fiber
materials are used which are not classified as carcinogenic according to
TRGS 905, class 1 or 2
- Tmax 1100 °C: Type
N thermocouple
- Tmax 1300 °C: Type
S thermocouple
- Frame for vertical
operation (RSV)
- Split-type design
for simple insertion of the working tube
- Working tube made
of material C 530 incl. fiber plugs for operation under air in scope of
delivery
- Heating elements on
support tubes provide for free radiation
- RSV: switchgear and
control unit separate from furnace in own wall or standing cabinet
- RSH: switchgear and
control unit integrated in furnace housing
- Defined application
within the constraints of the operating instructions
- NTLog Basic for
Nabertherm controller: recording of process data with USB-flash drive
Additional equipment
- Charge control with
temperature measurement in the working tube and in the furnace chamber
outside the tube
- Display of inner
tube temperature with additional thermocouple
- Different gas
supply systems for non-flammable or flammable protective or reactive gases
and vacuum operation
- Three-zone control
for optimization of temperature uniformity
- Cooling systems for
accelerated cooling of the working tube and charge
- Check valve at gas
outlet avoids intrusion of false air
- Base frame with
integrated switchgear and controller
- Process control and
documentation via VCD software package or Nabertherm Control Center (NCC)
for monitoring, documentation and control
Available
Model Number ; RSH 50/250/.., RSH 50/500/.., RSH 80/500/.., RSH 80/750/.., RSH 120/500/.,
RSH 120/750/., RSH 120/1000/, RSH 170/750/, RSH 170/1000/, RSV
50/250/.., RSV 50/500/., RSV 80/500/.., RSV 80/750/., RSV 120/500/, RSV
120/750/., RSV 120/1000/., RSV 170/750/.., RSV 170/1000/.
Rotary
Tube Furnaces for Batch Operation up to 1100 °C
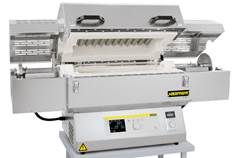 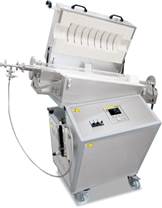 |
|
Rotary tube furnace RSRB 80/500/11 as tabletop version for
batch operation |
Rotary tube furnace RSRB 120/500/11 |
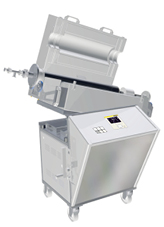
Rotary
tube furnace tilted towards the right side for charging and batch operation
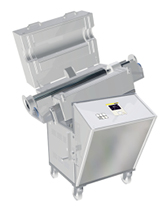
Rotary
tube furnace tilted towards the left side to discharge
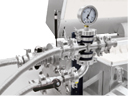
Connection
set for vacuum operation
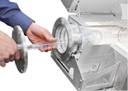
Gas tight
closing plug for tubes made of quartz glass closed at one side
The rotary tube furnaces of the RSRB series are ideally suited
for batch operation. The permanent rotation of the working tube ensures that
the charge is constantly in motion. Due to the special shape of the quartz
reactor with the tapered pipe ends the batch is kept in the rotary tube furnace
and can be heat-treated an arbitrarily long time period time; a controlled
heating to the temperature profiles is also possible.
- Tmax 1100 °C
- Thermocouple type K
- Dual shell housing
made of sheets of textured stainless steel
- Only fiber
materials are used which are not classified as carcinogenic according to
TRGS 905, class 1 or 2
- Tube furnace
designed as table-top model with quartz glass reactor which opens on both
sides, tapered ends
- Reactor is removed
for emptying out of the rotary tube furnace. Beltless drive and hinged
furnace housing (opening temperature < 180 °C) provide for very easy
removal through
- Adjustable drive of
approx. 2-45 rpm
- Switchgear and
control unit separate from tube furnace in own wall or standing cabinet
- Defined application
within the constraints of the operating instructions
- NTLog Basic for
Nabertherm controller: recording of process data with USB-flash drive
Additional equipment
- Three-zone control
for the optimization of temperature uniformity
- Temperature display
unit in the working tube with measurement by means of an additional
thermocouple
- Charge control by
means of an additional thermocouple in the working tube
- Different gassing
ensures good flushing of the charge with process gas through inlet on one
side and outlet on other side of tube
- Gas-tight rotary
feedthrough for connection of the rotating reactor to a gas supply system
- Check valve at gas
outlet avoids intrusion of false air
- Vacuum design, up
to 10-2 mbar depending on
the applied pump
- Open on both sides
reactor made of quartz glass with knobs for better mixing of the charge in
the tube
- Package for
improved charging and discharging of the working tube in the following
design:
- Mixing reactor
made of quartz glass with integrated blade for better mixing of the
batch, closed on one side, large opening on the other side
- Tilting mechanism
to the left/to the right. For charging and heat treatment, the furnace is
tilted towards the right side until the stop so that the load is charged
into the rotary tube furnace. For discharge, the furnace is tilted
towards the other side to discharge the powder from the reactor. It is no
longer necessary to remove the reactor.
- Rotary tube
furnace assembled on base with integrated switchgear and controller,
incl. transport casters
- Process control and
documentation via VCD software package or Nabertherm Control Center (NCC)
for monitoring, documentation and control
Available Model Number:
RSRB 80-500/11, RSRB 80-750/11, RSRB 120-500/11, RSRB 120-750/11, RSRB
120-1000/11
Rotary Tube Furnaces for Continuous
Processes up to 1300 °C
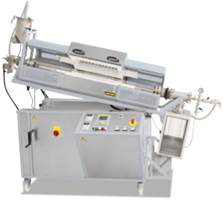 |
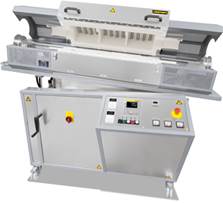 |
Rotary tube furnace RSRC 80/500/11 for processes under
protective gas or in vacuum |
Rotary tube furnace RSRC 120/750/13 |
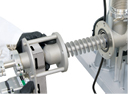
Screw-conveyor
with adjustable speed
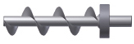
Screw-conveyors
with different pitches for the adaption to the charge
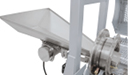
Vibrating
channel on the rotary tube for convenient material feeding
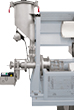
Vibration
generator at the charging funnel for improved powder supply
The RSRC rotary tube furnaces are particularly suitable for
processes where continuously running batch material is heated for a short time.
The rotary tube furnace is positioned slightly inclined
heated-up to the target temperature. The material is then continuously supplied
at the upper end of the tube. It passes through the heated area of the tube and
falls on the lower end out of the tube. The time of heat treatment results from
the inclination angle, the rotational speed and the length of the working tube,
as well as from the flow properties of the batch material.
Equipped with the optional closed loading system for 5 liter
charge material incl. receptacle, the rotary tube furnace can also be used for
processes under protective gas or vacuum.
Depending
on process, charge and required maximum temperature, different working tubes
made of quartz glass, ceramics or metal are used (see page 50). This rotary
tube furnace is therefore highly adaptable for different processes.
- Tmax 1100 °C
- Working tube made
of quartz glass open at both sides
- Thermocouple type
K
- Tmax 1300 °C
- Open tube made of
ceramics C 530
- Thermocouple type
S
- Heating elements on
support tubes provide for free radiation
- Dual shell housing
made of sheets of textured stainless steel
- Only fiber
materials are used which are not classified as carcinogenic according to
TRGS 905, class 1 or 2
- Adjustable drive of
approx. 2-45 rpm
- Digital display
unit for the tilting angle of the rotary tube furnace
- Beltless drive and
split-type furnace housing (opening temperature < 180 °C) provide for
very easy tube removal
- Compact system,
rotary tube furnace positioned on a base frame with
- Manual spindle
drive with crank to preset the tilting angle
- Switchgear and
controls integrated
- Castors
- Defined application
within the constraints of the operating instructions
- NTLog Basic for
Nabertherm controller: recording of process data with USB-flash drive
Additional equipment
- Three-zone control
for the optimization of temperature uniformity
- Temperature display
unit in the working tube with measurement by means of an additional
thermocouple
- Charge control by
means of an additional thermocouple in the working tube
- Different gassing
systems with good flushing of the charge with process gas (also possible
with hydrogen) in counterflow (only in combination with feeding system
below)
- Vacuum design, up
to 10-2 mbar depending on
the applied pump
- Vibrating channel
and extension piece on the rotary tube for convenient material
supply/removal, suitable for processes in normal atmosphere
- Charging system for
continuous material transport, consisting of:
- Stainless steel
funnel incl. electric vibration generator to optimize the material
feeding into the working tube
- Electrically
driven screw-conveyor at the inlet of the working tube with 10, 20 or
40 mm pitch and adjustable speed between 0.28 and 6 revolutions per
minute, different gear transmissions for other speeds on request
- Collecting bottle
made of laboratory glass at the outlet of the working tube
- Suitable for
operation in gas atmosphere or vacuum
- Working tubes made
of differents materials
- Quartz glass batch
reactors, Tmax 1100 °C
- Higher temperatures
up to 1500 °C available on request
- PLC controls for
temperature control and the control of connected aggregates such as
gearshift and speed of the screw-conveyor, speed of the working tube,
switching of the vibration generator, etc.
- Process control and
documentation via VCD software package or Nabertherm Control Center (NCC)
for monitoring, documentation and control
Available Model Number:
RSRC 80-500/11, RSRC 80-750/11, RSRC 120-500/11, RSRC 120-750/11, RSRC
120-1000/11, RSRC 80-500/13, RSRC 80-750/13, RSRC 120-500/13, RSRC 120-750/13,
RSRC 120-1000/13
Gas Supply Systems/Vacuum Operation
for Tube Furnaces
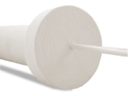
Gas supply
system 1: Fiber plugs with protective gas connection, suitable for many laboratory
applications
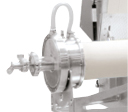
Water-cooled
stainless steel flange
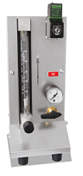
Gas supply
system for non-flammable protective or reactive gas with shutoff valve and flow
meter with regulator valve, optionally with magnetic valve
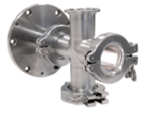
Observation
window as additional equipment for gas tight flanges
When equipped with various equipment packages, the tube furnace
product lines can be adapted for operation with nonflammable or flammable
gasses or for vacuum operation.
Gas Supply
System 1 for non-flammable protective or reactive gases Not gastight, no vacuum
operation
This package represents a basic version sufficient for many
applications, for operation with non-flammable protective or reactive gasses.
The standard working tube made of ceramic C 530 delivered with the furnace can
still be used.
- Available for tube
furnaces RD, R, RT, RSH and RSV
- Standard working
tube can be used
- 2 plugs made of
porous, non-classified ceramic fiber incl. protective gas connections
- Gas supply system
for nonflammable protective gas (Ar, N2, forming gas,
others on request) with shutoff valve and flow meter with control valve,
optionally with magnetic valve. One gas intake pressure at 300 mbar to be
provided by customer.
Additional equipment
- Extension of gas
supply system with a second or third nonflammable type of gas
- Bottle pressure
regulator for use with bottled gas
- Automatic switching
on/off by means of the program segments of the controller, only possible
with control systems which include programmable extra functions
Gas Supply System 2 for non-flammable protective or reactive
gases/vacuum operation
For increased atmospheric purity requirements in the working
tube, we recommend this gas supply system. The system can also be equipped for
vacuum operation.
- Available for tube
furnaces R, RSH, RSV, RSRB, RSRC, RHTC, RHTH, RHTV
- Gas supply system
for nonflammable protective gas (Ar, N2, forming gas,
others on request) with shutoff valve and flow meter with control valve,
optionally with magnetic valve. One gas intake pressure at 300 mbar to be provided
by customer.
- Additional
equipment for static tube furnaces:
- Longer, gas tight
working tube of ceramic C 610 for furnaces to 1300 °C or of C 799 for
temperatures above 1300 °C
- 2 vacuum-tight,
water-cooled stainless steel flanges with fittings on the outlet side
(cooling water supply with NW9 hose connector to be provided by the
customer)
- Mounting system on
furnace for the flanges
- Additional
equipment for RSRC models (continuous operation): charging system
- Additional
Equipment for RSRB models: gas-tight rotarylead-outs on gas inlet and
outlet, gas cooler and gas outlet valve
Additional equipment
- Extension of gas
supply system with a second or third nonflammable type of gas
- Bottle pressure
regulator for use with bottled gas
- Automatic switching
on/off by means of the program segments of the controller, only possible
with control systems which include programmable extra functions
- Gas-supply
programmable via mass-flow controllers (only in combination with
PLC-controls)
- Process tubes made
of different materials
- Quick-locks for
watercooled flanges
- Cooling unit for
closed loop water circuit
- Window for charge
observation in combination with gas tight flanges
Vacuum Operation
- Vacuum package for
evacuation of the working tube, consisting of connector for the gas
outlet, ball valve, manometer, manually operated rotary vane vacuum pump
with corrugated stainless steel hose connected to the gas outlet, max.
attainable end pressure in working tube depending on pump type
- Pumps for max.
final pressure of up to 10-5 mbar (models
RSRB/RSRC up to 10‑2 mbar) on request
- The decrease in
strength of the working tube at high temperatures limits the maximum
operating temperature under vacuum
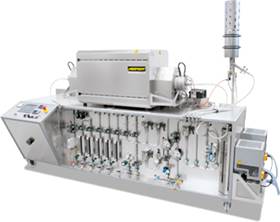
RHTH
120-600/18 with gas supply system4 for hydrogen operation
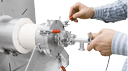
Water-cooled
end flange with quick connectors as additional equipment
Gas Supply
System 4 for hydrogen, fully-automatic, unattended operation
Adding gas supply system 4 to the tube furnace allows operation
under a hydrogen atmosphere. During hydrogen operation, a safety pressure of
approx. 30 mbar is ensured in the working tube. Surplus hydrogen is burnt off
in an exhaust gas torch. With extended safety logic and an integrated nitrogen
purge container, the system can be used for fully-automatic, unattended
operation. Equipped with a Safety-PLC control system, pre-purging, hydrogen
inlet, operation, fault monitoring and purging at the end of the process are
carried out automatically. In case of default, the tube is immediately purged
with nitrogen and the system is automatically switched to a safe status.
- Available for tube
furnaces RSH, RSV, RSRC, RHTH and RHTV
- Safety system for
operation with flammable gases including monitoring of torch function and
overpressure
- Extended safety
control system with emergency tube purging in case of default
- Emergency purge
container
- Safety-PLC control
system with touchpanel for data input
- Exhaust gas torch
- Pressure switch for
monitoring the safety pressure
- Gas supply system
for H2 and N2. Volume adjustment
is carried out by hand (the customer provides an H2 supply at 1
bar, an N2 supply at
10 bar, an O2 supply at 6-8 bar and a propan supply at 300 mbar)
Additional equipment
- Gas supply system
extension for additional nonflammable gas types
- Operation with
other flammable gases on request
- Bottle pressure
reducer for use with bottled gas
- Cooling unit for
closed loop water circuit
- Vacuum packages
(with hydrogen operation, this package can only be used for
pre-evacuation)
- Gas supply via
program-dependent, controllable mass flow controllers
Vacuum Pumps
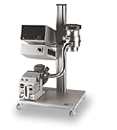
Vacuum
pump stand for operation up to 10
-5 mbar

Independent
pressure gauge for a pressure range of 10
-3 mbar or 10
-9 mbar
With respect to the final
pressure different pumps are available
- Single-step rotary
piston pump for a max. final pressure of approx. 20 mbar.
- Two-step rotary
piston pump for a max. final pressure of approx. 10-2 mbar.
- Turbomolecular pump
stand (rotary vane pump with following turbomolecular pump for a max.
final pressure of 10-5 mbar.
- Independent
pressure gauge for a pressure range of 10-3 mbar or 10-9 mbar as additional
equipment
Information:
For protection of the vacuum pump only cold stage evacuation is
allowed.
Control Alternatives for Tube
Furnaces
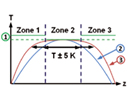
Three-Zone
Furnace Chamber Control
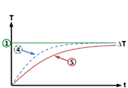
Furnace
control
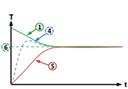
Charge
control
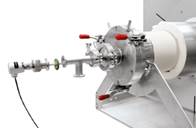
Thermocouple
for charge control in the RHTH 120/600/18 furnace
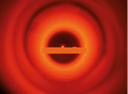
Sintering
under hydrogen in a tube furnace of RHTH product line
Three-Zone
Furnace Chamber Control
The temperature is measured by thermocouples positioned outside
of the working tube, one in the middle and two on the sides. The outer zones
are controlled with a setpoint-offset in relation to the middle zone. This
allows the heat loss at the ends of the tube to be compensated to ensure an
extended zone of constant temperature (+/- 5 K).
Furnace Chamber Control with
temperature measurement in furnace chamber outside the working tube.
- Advantages:
Thermocouple protected against damage and aggressive load, very even
control, attractive price
- Disadvantage:
Temperature difference between displayed temperature on the controller and
inside the tube
Extension Package for Furnace
Chamber Control
- with additional
temperature measurement in the working tube and display of the measured
temperature
- Advantages: Very
precise and rapid control adjustment
- Disadvantage: Costs
Furnace Chamber vs. Charge Control Comparison
Furnace
Chamber Control
Only the furnace chamber temperature is measured and controlled.
Regulation is carried out slowly to avoid out-of-range values. As the charge
temperature is not measured and controlled, it may vary a few degrees from the
chamber temperature.
Charge
Control
If the charge control is switched on, both the charge
temperature and furnace chamber temperature are measured. By setting different
parameters the heat-up and cooling processes can be individually adapted. This
results in a more precise temperature control at the charge.
Customized Tube Furnaces
Working Tubes for Tube Furnaces
Melting Furnaces up to 1500 °C
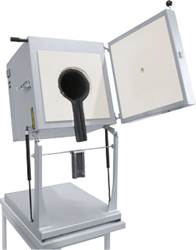 |
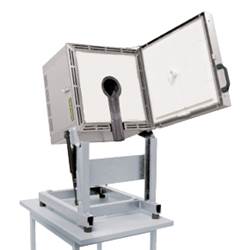 |
Melting furnace K 4/10 |
Melting furnace KC 2/15 |
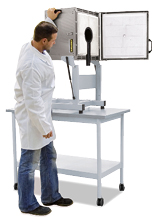
Melting
furnace KC 2/15
These compact melting furnaces for the melting of non-ferrous
metals and alloys are one of a kind and have a number of technical advantages.
Designed as tabletop models, they can be used for many laboratory applications.
The practical counter balanced hinge with shock absorbers and the spout (not
for KC) on the front of the furnace make exact dosing easy when pouring the
melt. The melting furnaces are available for furnace chamber temperatures of
1000, 1300, or 1500 °C. This corresponds to melt temperatures of about
80 °C - 110 °C lower.
- Tmax 1000 °C, 1300
°C, or 1500 °C, with melt temperature about 80 °C - 110 °C lower
- Crucible sizes of
0,75, 1,5 or 3 liters
- Crucible with
integrated pouring spout of iso-graphite included with delivery
- Additional spout
(not for KC), mounted at the furnace for exact pouring
- Compact bench-top
design, simple emptying of crucible by tiltiing system with gas damper
- Crucible for
heating up of melting furnace insulated with a hinged lid, lid opened when
pouring
- Defined application
within the constraints of the operating instructions
Additional equipment
- Other crucible
types available, e.g. steel
- Design as bale-out
furnace without tilting device, e.g. for lead melting
- Over-temperature
limiter for the furnace chamber with automatic reset to protect against
overtemperature. The limit controller switches off the heating when the
pre-set limit temperature has been reached and does not switch it on again
until the temperature falls below the setting again.
- Observation hole
for melt
Available
Model Number: K 1/10, K 2/10, K 4/10, K 1/132, K 2/132, K 4/132, KC 1/153, KC 2/153
Fast-Firing Furnaces up to 1300 °C
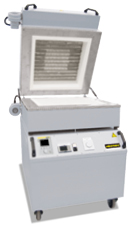
|
Fast-firing furnace LS 25/13
|
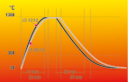
Firing curves of fast-firing furnaces LS 12/13 and LS 25/13
These
fast-firing furnaces are ideal for simulation of typical fast-firing processes
up to a maximum firing temperature of 1300 °C. The combination of high
performance, low thermal mass and powerful cooling fans provides for cycle
times from cold to cold up to 35 minutes with an opening temperature of approx.
300 °C.
- Tmax 1300 °C
- Very compact design
- Ceramic grid tubes
as charge support
- Floor and lid
heating
- Two-zone control,
bottom and lid
- Integrated cooling
fans, programmable to speed up charge cooling including housing cooling
- Programmable lid
opening of approximately 60 mm for faster cooling without activating the
fan
- Thermocouple type S
for top and bottom zone
- Castors for easy
furnace moving
- Defined application
within the constraints of the operating instructions
- NTLog Basic for
Nabertherm controller: recording of process data with USB-flash drive
Available Model Number:
LS 12/13, LS 25/13
Gradient or Lab Strand Annealing Furnaces up to 1300 °C
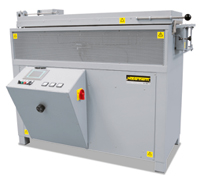 |
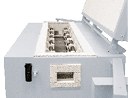 |
Gradient furnace GR 1300/13S |
Furnace chamber of gradient furnace GR 1300/13 with
second door as additional equipment |
The furnace chamber of the gradient furnace GR 1300/13 is
divided in six control zones of equal length. The temperature in each of the
six heating zones is separately controlled. The gradient furnace is usually
charged from the side through the parallel swivel door. A maximum temperature
gradient of 400 °C can then be stabilized over the heated length of 1300 mm. On
request the furnace also is designed as a lab strand annealing furnace with a
second door on the opposite side. If the included fiber separator are used
charging is carried-out from the top.
- Tmax 1300 °C
- Heated length: 1300
mm
- Heating elements on
support tubes providing for free heat radiation in the kiln chamber
- Charging from the
top or through the right side door
- Gas damper
suspension of the lid
- 6-zone control
- Separate control of
heating zones (each 160 mm long)
- Temperature
gradient of 400 °C over the entire length of the kiln chamber, each zone
can individually be controlled
- Fiber separators
dividing the chamber in six equally sized chambers
- Defined application
within the constraints of the operating instructions
Additional equipment
- Up to ten control
zones
- Second parallel
swivel door for use as lab strand annealing furnace
- Vertical instead of
horizontal strand furnace
- Process control and
documentation via Nabertherm Control Center (NCC) for monitoring,
documentation and control
Available Model Number:
GR 1300/13
Retort Furnaces
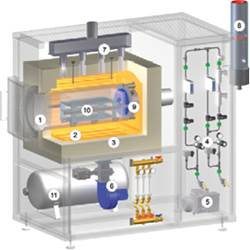 |
Schematic presentation of a hot-wall retort
furnace with additional equipment 1 Retort 2 Heating 3 Insulation 4 Gas
management system 5 Vacuum pump 6 Fan for indirect cooling 7 Outlet indirect
cooling 8 Exhaust torch 9 Fan for gas circulation (NRA models) 10 Charging
frame 11 Emergency flushing container
|
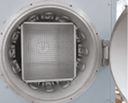
Inside
heating in retort furnaces NRA ../06
These gas tight retort furnaces are equipped with direct or
indirect heating depending on temperature. They are perfectly suited for
various heat treatment processes requiring a defined protective or a reaction
gas atmosphere. These compact models can also be laid out for heat treatment
under vacuum up to 600 °C. The furnace chamber consists of a gas tight retort
with water cooling around the door to protect the special sealing. With the
corresponding safety technology, retort furnaces are also suitable for
applications under reaction gases, such as hydrogen or, in combination with the
IDB package, for inert debinding or for pyrolysis processes.
Different model versions are available depending on the
temperature range:
Models NRA ../06 with Tmax 650 °C
- Heating elements
located inside the retort
- Temperature
uniformity up to +/- 5 °C inside the work space
- Retort made of
1.4571
- Gas circulation fan
in the back of the retort provides for optimal temperature uniformity
- Insulation made of
mineral wool
Models NRA ../09 with Tmax 950 °C
- Design like models
NRA ../06 with following differences:
- Outside heating
with heating elements around the retort
- Retort made of
1.4828
- Only fiber
materials are used which are not classified as carcinogenic according to
TRGS 905, class 1 or 2
Models NR ../11 with Tmax 1100 °C
- Design like models
NRA ../09 with following differences:
- Retort made of
1.4841
- Without
gas-circulation
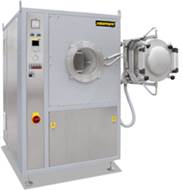 |
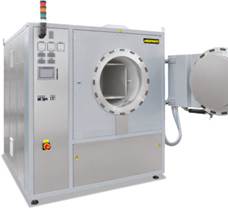 |
Retort furnace NRA 25/09 |
Retort furnace NRA 150/09 with controls H1700 and bayonet door
lock |
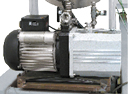
Vacuum pump
for cold evacuation of the retort
Basic version
- Compact housing in
frame design with removable stainless steel sheets
- Controls and gas
supply integrated in the furnace housing
- Welded charging
supports in the retort resp. air-baffle box in the furnaces with
atmosphere circulation
- Swivel door hinged
on right side
- Open cooling water
system
- Depending on
furnace volume for 950 °C- and 1100 °C-models the control system is
divided in one or more heating zones
- Furnace temperature
control with measurement outside the retort
- Gas supply system
for one non-flammable protective or reaction gas with flow meter and
magnetic valve
- Port for vacuum
pump for cold evacuation
- Operation under
vacuum up to 600 °C with optional single-stage rotary vane pump
- Defined application
within the constraints of the operating instructions
- NTLog Basic for
Nabertherm controller: recording of process data with USB-flash drive
Additional equipment
- Upgrade for other
non-flammable gases, H2 version for flammable gases
- Automatic gas
injection, including MFC flow controller for alternating volume flow,
controlled with process control H3700, H1700
- Vacuum pump for
evacuating of the retort up to 600 °C, attainable vacuum up to 10-5 mbar subject to
selected pump
- Indirect cooling
- Direct cooling
- Heat exchanger with
closed-loop cooling water circuit for door cooling
- Measuring device
for residual oxygen content
- Door heating
- Temperature control
as charge control with temperature measurement inside and outside the
retort
- Retort, made of
2.4633 for Tmax 1150 °C
- Process control and
documentation via VCD software package or Nabertherm Control Center (NCC)
for monitoring, documentation and control
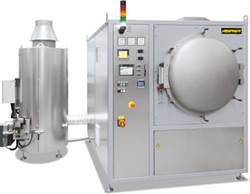
|
Retort furnace NRA 400/03 IDB
with thermal post combustion system
|
IDB Version for Debinding under Non-flammable Protective Gases
or for Pyrolysis Processes
The retort
furnaces of the NR and NRA product line are perfectly suited for debinding
under non-flammable protective gases or for pyrolysis processes. The IDB
version of the retort furnaces implements a safety concept by controlled
inerting the furnace chamber with a protective gas. Exhaust gases are burned in
a termal post combustion. Both the purging and the torch function are monitored
to ensure a safe operation.
- Process control
under monitored overpressure
- Process control
H1700 with PLC controls and graphic touch panel for data input
- Monitored gas
pre-pressure of the process gas
- Bypass for safe
flushing of furnace chamber with inert gas
- Thermal post
combustion of exhaust gases
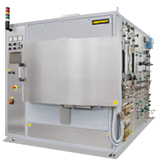
|
Retort furnace NRA 300/09 H2 for heat
treatment under hydrogen
|
H2 Version
for Operation with Flammable Process Gases
When a
flammable process gas like hydrogen is used, the retort furnace is additionally
equipped with the required safety technology. Only certified and industry
proven safety sensors are used. The furnace is controlled by a fail-safe PLC
control system (S7- 300F/safety controller).
- Supply of flammable
process gas at controlled overpressure of 50 mbar relative
- Certified safety
concept
- Process control
H3700 with PLC controls and graphic touch panel for data input
- Redundant gas inlet
valves for hydrogen
- Monitored
pre-pressures of all process gases
- Bypass for safe
flushing of furnace chamber with inert gas
- Torch for thermal
post combustion of exhaust gases
- Emergency flood
container for purging the furnace in case of failore
Available Model Number:
NRA 17/.., NRA 25/.., NRA 50/.., NRA 75/.., NRA 150/., NRA
200/.., NRA 300/.., NRA 400/.., NRA 500/.., NRA 700/.., NRA 1000/..
Bottom Loading Retort Furnaces up to
1100 °C
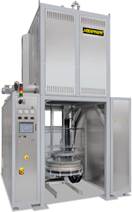 |
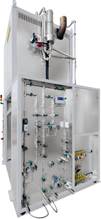 |
Bottom loading retort furnace LBR 300/11 H2 with safety technology
for operation with Hydrogen as process gas |
Gas management system at bottom loading retort furnace LBR
300/11 H2 |
The bottom
loading retort furnaces of the LBR series are suitable for production processes
that are carried out in protective/reaction gas atmosphere. With regard to the
basic performance data, these models are constructed like the SR models. Their
size and design with electro-hydraulically driven lifting bottom make it easier
to load heavy duties. The retort furnaces are available in different sizes and
designs.
Basic version (all models)
- Tmax 650 °C, 950 °C
or 1100 °C
- Frame-mounted
housing with stainless steel sheets
- Charging from the
front
- Electro-hydraulically
driven furnace bottom
- Gas supply system
for a non-flammable protective gas or reaction gas with flow meter and
solenoid valve
- Temperature control
designed as furnace chamber control
- Connection possibility
for an optional vacuum pump (cold evacuation or operation up to 600 °C
under vacuum)
- Defined application
within the constraints of the operating instructions
- NTLog Basic for
Nabertherm controllers: recording of process data with USB flash drive
- Additional
equipment, H2 version and
IDB version see models NR and NRA
Cold-Wall Retort Furnaces up to 2400
°C or up to 3000 °C
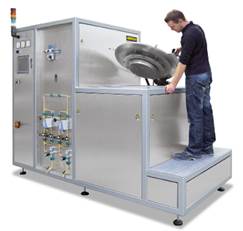 |
Retort furnace SVHT 9/24-W with tungsten heating |
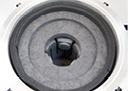
Graphite
heating module
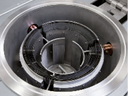
Cylindrical
retort with tungsten heating
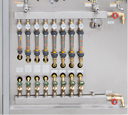
Cooling
water distribution
Compared with the VHT models (page 64 ff), the retort furnaces
of the SVHT product line offer improved performance data with regard to
achievable vacuum and maximum temperature. Due to the design as pit-type
furnace with tungsten heating, processes up to max. 2400 °C even in high vacuum
can be implemented with retort furnaces of the SVHT..-W product line. Retort
furnaces of the SVHT..-GR product line with graphite heating, also in pit-type
design, can be operated in an inert gas atmosphere even up to max. 3000 °C.
- Standard sizes with
a furnace chamber of 2 or 9 liters
- Designed as
pit-type furnace, charged from above
- Frame construction
with inserted sheets of textured stainless steel
- Dual shell
water-cooled stainless steel container
- Manual operation of
process gas and vacuum functions
- Manual gas supply
for non-combustible process gas
- A step in front of
the retort furnace for an ergonomic charging height
- Retort lid with
gas-charged shock absorbers
- Controls and
switchgear as well as gas supply integrated in furnace housing
- Defined application
within the constraints of the operating instructions
- Further standard
product characteristics see description for standard design of VHT models
Heating Options
SVHT ..-GR
- Applicable for
processes:
- Under protective
or reaction gases or in the vacuum up to 2200 °C under consideration of
relevant max. temperature limits
- Under inert gas
argon up to 3000 °C
- Max. vacuum up to
10-4 mbar depending on
the type of pump used
- Heating: graphite
heating elements in cylindrical arrangement
- Insulation:
graphite felt insulation
- Temperature
measurement by means of an optical pyrometer
SVHT ..-W
- Applicable for
processes under protective or reaction gases or in vacuum up to 2400 °C
- Max. vacuum up to
10-5 mbar depending on
the type of pump used
- Heating:
cylindrical tungsten heating module
- Insulation:
tungsten and molybdenum radiant plates
- Optical temperature
measurement with pyrometer
- Additional
equipment such as automatic process gas control or design for the
operation with flammable gases incl. safety system see VHT models
Available Model Number:
SVHT 2/24-W, SVHT 9/24-W, SVHT 2/30-GR, SVHT 9/30-GR
Cold-Wall Retort Furnaces up to 2400
°C
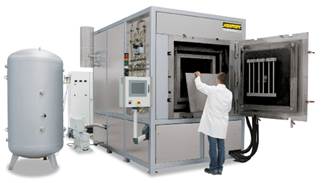 |
Retort furnace VHT 500/22-GR H2 with CFC-process box and
extension package for operation under hydrogen |
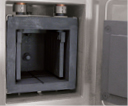
Graphite
heating chamber
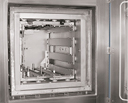
Molybdenum
or tungsten heating chamber
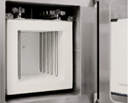
Molybdenumdisilicide
heater and fiber insulation
The compact retort furnaces of the VHT product line are
available as electrically heated chamber furnaces with graphite, molybdenum,
tungsten or MoSi
2 heating. A wide variety of heating designs as
well as a complete range of accessories provide for optimal retort furnace
configurations even for sophisticated applications.
The vacuum-tight retort allows heat treatment processes either
in protective and reaction gas atmospheres or in a vacuum, subject to the
individual furnace specs to 10
-5 mbar. The
basic furnace is suited for operation with non-flammable protective or reactive
gases or under vacuum. The H
2 version
provides for operation under hydrogen or other flammable gases. Key of the
specification up is a certified safety package providing for a safe operation
at all times and triggers an appropriate emergency program in case of failure.
Alternative
Heating Specifications
In general the following variants are available wit respect to
the process requirements:
VHT ../..-GR with Graphite
Insulation and Heating
- Suitable for
processes under protective and reaction gases or under vacuum
- Tmax 1800 °C
, 2200 °C or 2400 °C (VHT 40/.. - VHT 100/..)
- Max. vacuum up to
10-4 mbar depending on
pump type used
- Graphite felt
insulation
VHT ../..-MO or VHT ../..-W with
Molybdenum or Tungsten Heating
- Suitable for
high-purity processes under protective and reaction gases or under high
vacuum
- Tmax 1200 °C,
1600 °C or 1800 °C (see table)
- Max. vacuum up to
10-5 mbar depending on
pump type used
- Insulation made of
molybdenum rsp. tungsten radiation sheets
VHT ../..-KE with Fiber
Insulation and Heating through Molybdenum Disilicide Heating Elements
- Suitable for
processes under protective and reaction gases, in air or under vacuum
- Tmax 1800 °C
- Max. vacuum up to
10-2 mbar (up to
1300 °C) depending on pump type
- Insulation made of
high purity aluminum oxide fiber
- Only fiber
materials are used which are not classified as carcinogenic according to
TRGS 905, class 1 or 2
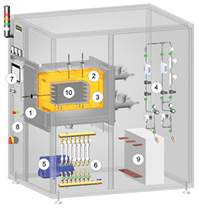 |
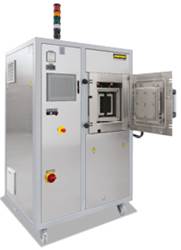 |
Schematic presentation of a cold-wall retort furnace with
additional equipment 1 Retort 2 Heating 3 Insulation 4 Gas management system
5 Vacuum pump 6 Cooling water distribution 7 Controls 8 Integrated switchgear
9 Heating transformer 10 Charging frame inside the inner process chamber |
Retort furnace VHT 8/16‑MO with automation package |
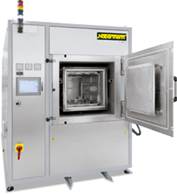
Retort
furnace VHT 100/16‑MO with automation package
Basic version
- Standard furnace
sizes 8 - 500 liters
- Water-cooled retort
made of stainless steel
- Frame made of
stable steel profiles, easy to service due to easily removable stainless
steel panels
- Housing of the VHT
8 model on castors for easy repositioning of furnace
- Cooling water
manifold with manual tap, automatic flow monitoring, open-loop cooling
water system
- Adjustable cooling
water circuits with flowmeter and temperature indicator and
overtemperature protection
- Switchgear and
controller integrated in furnace housing
- Process control
with controller P470
- Over-temperature
limiter with adjustable cutout temperature for thermal protection class 2
in accordance with EN 60519-2
- Manual operation of
the process gas and vacuum functions
- Manual gas supply
for one process gas (N2 , Ar or non-flammable forming gas) with
adjustable flow
- Bypass with manual
valve for rapid filling or flooding of furnace chamber
- Manual gas outlet
with overflow valve (20 mbar relative) for over-pressure operation
- Single-stage rotary
vane pump with ball valve for pre-evacuating and heat treatment in a rough
vacuum to 5 mbar
- Pressure gauge for
visual pressure monitoring
- Defined application
within the constraints of the operating instructions
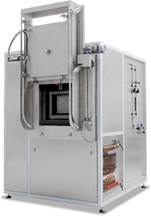 |
Retort furnace VHT 40/22-GR with motor-driven lift door and
front frame for connection to a glovebox |
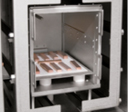
Heat
treatment of copper bars under hydrogen in retort furnace VHT 8/16-MO
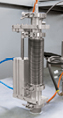
Thermocouple,
type S with automatic pull-out device for precise control results in the low
temperature range
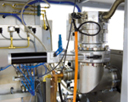
Turbo-molecular
pump
Additional equipment
housing/heater
- Housing, optionally
divisible, for passing through narrow door frames (VHT 8)
- Lift door
- Individual heating
concepts
Additional equipment gas
management system
- Manual gas supply
for second process gas (N2, Ar or non-flammable forming gas) with
adjustable flow and bypass
- Mass flow
controller for alternating volume flow and generation of gas mixtures with
second process gas (only with automation package)
- Inner process box
made of molybdenum, tungsten, graphite or CFC, especially recommended for
debinding processes. The box is installed in the furnace with direct gas
inlet and outlet and provides for better temperature uniformity. Generated
exhaust gases will be directly lead out the inner process chamber during debinding.
The change of gas inlet pathes after debinding results in a clean process
gas atmosphere during sintering.
Additional equipment vacuum
- Two-stage rotary
vane pump with ball valve for pre-evacuating and heat-treating in a fine
vacuum (up to 10-2 mbar) incl.
electronic pressure sensor
- Turbo molecular
pump with slide valve for pre-evacuation and for heat treatment in a high
vacuum (up to 10-5 mbar)
including electronic pressure sensor and booster pump
- Other vacuum pumps
on request
- Partial pressure
operation: protective gas flushing at controlled underpressure (only with
automation package)
Additional equipment cooling
- Heat exchanger with
closed-loop cooling water circuit
- Direct cooling
Additional equipment for controls
and documentation
- Charge thermocouple
with display
- Temperature
measurement at 2200 °C models with pyrometer in the upper
temperature range and thermocouple, type C with automatic pull-out device
for precise control results in the low temperature range (VHT 40/..-GR and
larger)
- Automation package
with process control H3700
- 12" graphic touch
panel
- Input of all
process data like temperatures, heating rates, gas injection, vacuum at
the touch panel
- Display of all
process-relevant data on a process control diagram
- Automatic gas
supply for one process gas (N2, argon or non-flammable forming
gas) with adjustable flow
- Bypass for
flooding and filling the chamber with process gas controlled by the
program
- Automatic pre- and
post programs, including leak test for safe furnace operation
- Automatic gas
outlet with bellows valve and overflow valve (20 mbar relative) for
over-pressure operation
- Transducer for
absolute and relative pressure
- Process control and
documentation via VCD software package or Nabertherm Control Center (NCC)
for monitoring, documentation and control
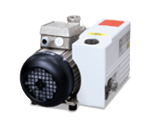
|
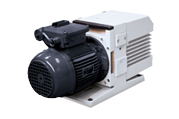
|
Single-stage rotary vane pump
for heat treatment in a rough vacuum to 5 mbar
|
Two-stage rotary vane pump for
heat treatment in a vacuum to 10-2 mbar
|

Graphite inner process chamber incl. charge holder
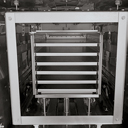
Molybdenum inner process chamber incl. six charge supports
Process Box for Debinding in Inert Gas
Certain
processes require charges to be debinded in non-flammable protective or
reactive gases. For these processes we fundamentally recommend a hot-wall retort
furnace (see models NR .. or SR ..). These retort furnaces can ensure
that the formation of condensation will be avoided as throughly as possible.
If there
is no way to avoid the escape of small amounts of residual binder during the
process, even in the VHT furnace, the retort furnace should be designed to meet
this contingency.
The
furnace chamber is equipped with an additional process box that has a direct
outlet to the exhaust gas torch through which the exhaust gas can be directly
vented. This system enables a substantial reduction in the amount of furnace
chamber contamination caused by the exhaust gases generated during debinding.
Depending
on the exhaust gas composition the exhaust gas line can be designed to include
various options.
- Exhaust gas torch
for burning off the exhaust gas
- Condensation trap
for separating out binding agents
- Exhaust gas
post-treatment, depending on the process, via exhaust gas washer
- Heated exhaust gas
outlet to avoid condensation deposits in the exhaust gas line
Available Model Number:
VHT 8/..., VHT 25/.., VHT 40/.., VHT 70/., VHT 100/.., VHT 250/.., VHT
500/.. ,
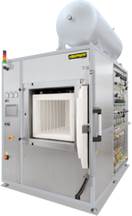 |
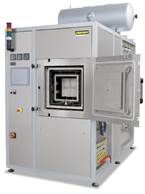 |
Retort furnace VHT 100/15-KE H2 with fiber insulation and
extension package for operation under hydrogen, 1400 °C |
Retort furnace VHT 40/16-MO H2 with hydrogen extension
package and process box |
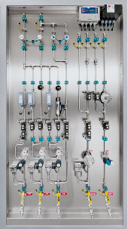
Gas
management system
H2 Version
for Operation with Hydrogen or other Reaction Gases
In the H
2 version the retort furnaces
can be operated under hydrogen or other reaction gases. For these applications,
the systems are additionally equipped with the required safety technology. Only
certified and industry proven safety sensors are used. The retort furnaces are
controlled by a fail-safe PLC control system (S7-300F/safety controller).
- Certified safety
concept
- Automation package
- Redundant gas inlet
valves for hydrogen
- Monitored
pre-pressures of all process gases
- Bypass for safe
purging of furnace chamber with inert gas
- Pressure-monitored
emergency flooding with automated solenoid valve opening
- Electrically heated
or gas-fired exhaust gas torch for H2 post combustion
- Atmospheric
operation: H2-purging of retort
starting from room temperature at controlled over pressure (50 mbar
relative)
Additional equipment
- Partial pressure
operation: H2 flushing at
underpressure in the retort starting from 750 °C furnace chamber
temperature
- Inner process hood
in the retort for debinding under hydrogen
- Process control and
documentation via Nabertherm Control Center (NCC) for monitoring,
documentation and control
Catalytic and Thermal Post Combustion
Systems, Exhaust Gas Washer
Temperature Uniformity and System Accuracy
Process Control and Documentation
Product-Videos